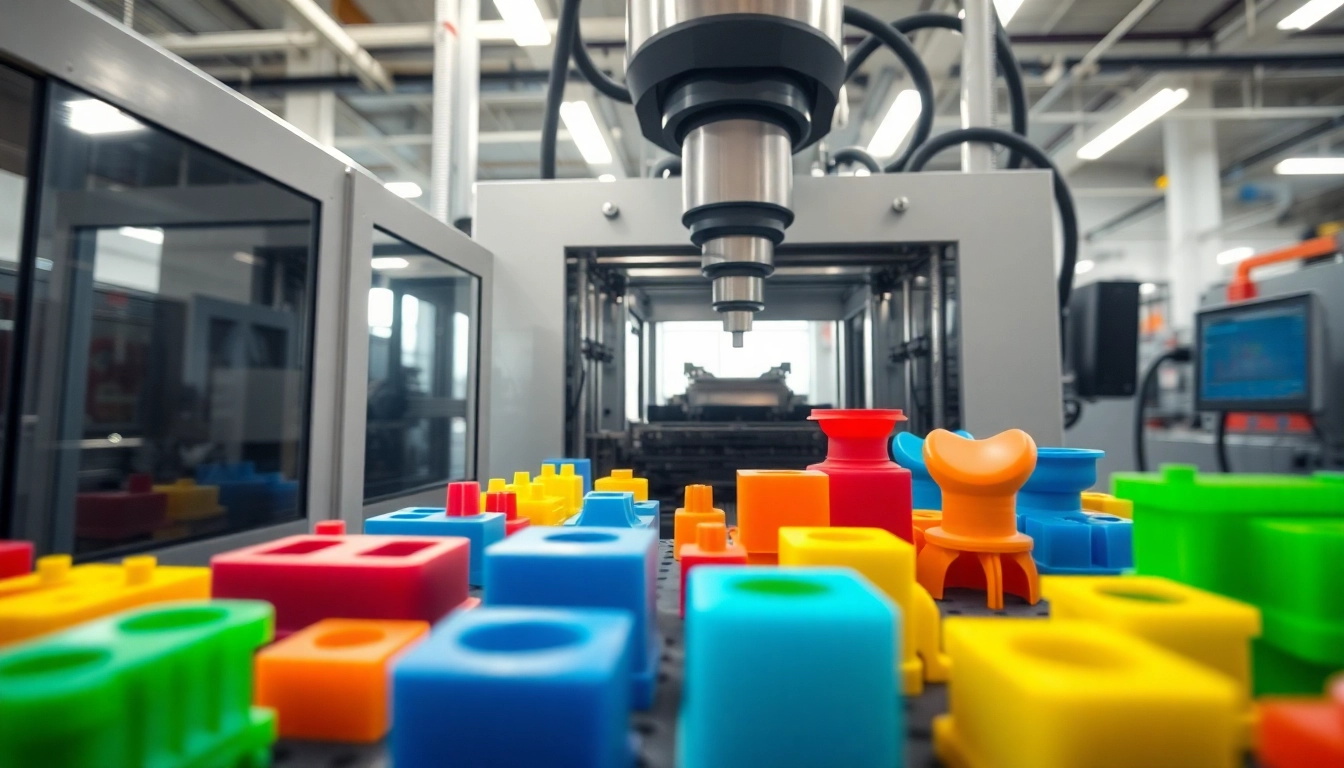
Understanding Injection Molding Prototypes
What Are Injection Molding Prototypes?
Injection molding prototypes serve as critical precursors in the manufacturing process, designed to test and validate product concepts before full-scale production. In essence, these prototypes are created using traditional injection molding techniques to provide insights into the final product’s design, material compatibility, and overall functionality. Unlike initial conceptual models made from methods like 3D printing, injection molding prototypes allow for a higher degree of accuracy and fidelity to the final product specifications.
This form of prototyping enables manufacturers to address design flaws, assess manufacturability, and refine product functionality. The prototypes can be made from various plastics, allowing designers to choose materials that best suit their needs while providing a realistic representation of the end product. Those interested in the nuances of this process will find it beneficial to explore injection molding prototypes further, as it encapsulates the essence of product design in modern manufacturing.
Benefits of Using Prototypes in Product Development
The significance of utilizing injection molding prototypes in product development cannot be overstated. Some notable advantages include:
- Early Detection of Design Flaws: Prototypes help in identifying potential issues in the design phase, significantly reducing costs and time associated with revisions later in the process.
- Functional Testing: They allow for hands-on testing to evaluate the product’s performance under real-world conditions, addressing functional and ergonomic issues before mass production.
- Material Evaluation: Different materials can be tested to determine the best fit for durability, appearance, and overall product life cycle.
- Market Testing: Prototypes can be utilized for consumer testing and feedback, providing insights into market trends and consumer preferences that inform design modifications.
- Time Efficiency: Rapid prototyping capabilities allow products to move from concept to production-ready status faster, giving companies a competitive edge in the marketplace.
Key Concepts in Prototype Injection Molding
Understanding the key concepts surrounding prototype injection molding provides a better framework for leveraging its advantages. Some essential elements include:
- Rapid Tooling: A method that uses simpler and less expensive molds designed specifically for low-volume production, enabling quicker turnaround times for prototypes.
- Material Selection: The choice of materials is crucial, as different plastics exhibit varying properties like strength, flexibility, and thermal resistance which directly influence the product’s success.
- Mold Design: The design of the mold used in injection molding is pivotal to ensure precise replication of the prototype, affecting timelines and costs.
- Quality Control Measures: Prototype production incorporates strict quality checks to ensure that tolerances and specifications are met, which predictably extends to full production runs.
Choosing the Right Materials for Prototypes
Material Options for Injection Molding
Material selection is integral to achieving the desired performance characteristics of injection molding prototypes. Each material offers unique benefits such as:
- ABS (Acrylonitrile Butadiene Styrene): This elastomer is known for its toughness and impact resistance, making it suitable for consumer products and automotive components.
- Polycarbonate: Excellent for products requiring transparency and high impact resistance, often used in eyewear lenses and safety equipment.
- PP (Polypropylene): Recognized for its chemical resistance and fatigue resistance, it’s commonly used in packaging and automotive applications.
- PVC (Polyvinyl Chloride): Highly versatile, PVC can be formulated to be rigid or flexible and is widely used in plumbing and electrical applications.
- POM (Polyoxymethylene): Known for its high stiffness and low friction properties, POM is ideal for precision engineering like gears and bearings.
Comparative Analysis of Plastics Used
When selecting materials for prototype injection molding, factors such as cost, mechanical properties, and processing ease must be compared. For instance, while ABS and POM might appear similar in terms of strength, their respective impact resistance and flexibility make them suited for different applications. Additionally, the molding process could require adjustments based on the mold temperature and cooling rates specific to each type of plastic.
Factors Influencing Material Selection
Several factors should inform the material selection process for injection molding prototypes, including:
- Cost Considerations: Evaluating the budget for materials while also considering the long-term performance and durability of the chosen plastic.
- Product Functionality: Understanding the functional requirements the product must meet, such as heat resistance for automotive parts or flexibility for housings.
- Regulatory Compliance: Given that some industries require compliance with specific regulations (like food safety standards), it is essential to ensure materials meet those criteria.
- Production Volume: Depending on whether the project requires low or high volumes, the materials might differ, influencing cost and efficiency.
The Injection Molding Process Explained
Steps in Prototype Injection Molding
The injection molding process for prototypes consists of several stages, including:
- Design and Planning: Involves creating a 3D CAD model of the prototype and planning the injection molding process, including mold design.
- Mold Creation: The manufacturing of the mold is either through traditional machining methods or rapid tooling processes to create an effective, cost-efficient mold.
- Material Selection: Finalize the choice of material based on the intended use of the prototype.
- Injection Molding: The selected plastic material is heated until molten and injected into the mold where it takes the shape of the design.
- Cooling and Ejection: The part is cooled and solidified inside the mold before being ejected to complete the process.
- Post-Processing: Involves any additional treatments like finishing touches, assembly, or quality assurance checks before delivering the prototype.
Common Techniques and Tools
To facilitate effective prototype injection molding, specific techniques and tools are implemented, including:
- Hot Runner Systems: Enhance the efficiency of the molding process by reducing material waste and allowing for better control of melt temperature.
- CNC Machining: Used to produce high-precision molds essential for fabricating injection-molded prototypes with stringent tolerance requirements.
- Quality Control Tools: Instruments like digital calipers and CMM (Coordinate Measuring Machines) ensure the prototypes meet the specified standards and tolerances.
Assessing Quality in Prototypes
Quality assessment is a vital step in the prototype evaluation process, ensuring that all specifications meet the required standards. Key performance metrics include:
- Dimensional Accuracy: Verify that all dimensions of the prototype align with design specifications, preventing issues during full-scale production.
- Surface Finish: The quality of the surface finish affects aesthetics and functionality; thus, prototypes must undergo visual inspections and testing.
- Material Properties: Evaluate how the chosen material behaves under stress, temperature variations, and other environmental factors relevant to the prototype’s function.
Cost Considerations in Injection Molding Prototypes
Budgeting for Prototype Production
Creating prototypes through injection molding can vary significantly in cost based on various factors such as:
- Mold Complexity: More intricate mold designs require greater investment in terms of both time and money.
- Material Costs: High-quality plastics may incur additional costs, impacting the overall budget.
- Production Volume: Although prototypes typically involve lower volumes, understanding the scaling of production might influence initial budgeting.
Thus, creating a detailed budget that outlines anticipated costs at each stage of the production process is critical for successful financial planning.
Understanding Cost vs. Value
When assessing the costs involved in prototype production, it is essential to differentiate reality from perceived value. While initial costs may appear high, the long-term value derived from successful prototyping—through reduced time to market, increased product success rates, and minimized risk of design flaws—must be taken into account. Companies often find that investing in quality prototypes leads to higher returns in final product performance and customer satisfaction.
Ways to Reduce Costs without Compromising Quality
Companies can implement several strategies to optimize costs while maintaining production quality:
- Utilizing Simplified Mold Designs: Employing simpler designs can lower production costs significantly and reduce lead times.
- Material Optimization: By selecting less expensive yet suitable materials, companies can dramatically cut costs without sacrificing functionality.
- Batch Production: Producing prototypes in smaller batches can help limit costs while still obtaining necessary data for quality assessments.
Best Practices for Efficient Use of Prototypes
Implementing Prototypes in Your Workflow
Integrating prototypes within product development workflows requires strategic planning and execution. Companies should consider:
- Establishing Clear Objectives: Define expectations of what will be learned or tested during the prototyping phase.
- Cross-Functional Collaboration: Involve various departments (engineering, marketing, etc.) in discussions to obtain a well-rounded perspective on the prototypes.
- Frequent Iterations: Encourage revisiting and revising prototypes based on testing feedback to refine the final product continually.
Case Studies of Successful Prototype Implementations
Examining case studies where successful iterations of injection molding prototypes propelled products forward can provide insight into effective strategies. For instance, one sporting goods manufacturer used injection molding prototypes to drastically decrease the development timeline of a new line of athletic shoes. Through iterative testing and rapid modifications, they identified optimal material characteristics and design features that resonated with their target audience, ultimately surging ahead of competitors.
Future Trends in Prototype Injection Molding
The future of prototype injection molding is evolving, shaped by advancements in technology and materials. Notable trends include:
- Increased Automation: Automation in robotic machining and molding processes will reduce labor costs and production time while enhancing precision.
- Sustainable Practices: The push towards sustainability is influencing materials selection, promoting biodegradable and eco-friendly plastics in prototype development.
- Integration of AI and Machine Learning: These technologies can optimize product designs through predictive analysis and enhance modeling accuracy during the injection molding process.