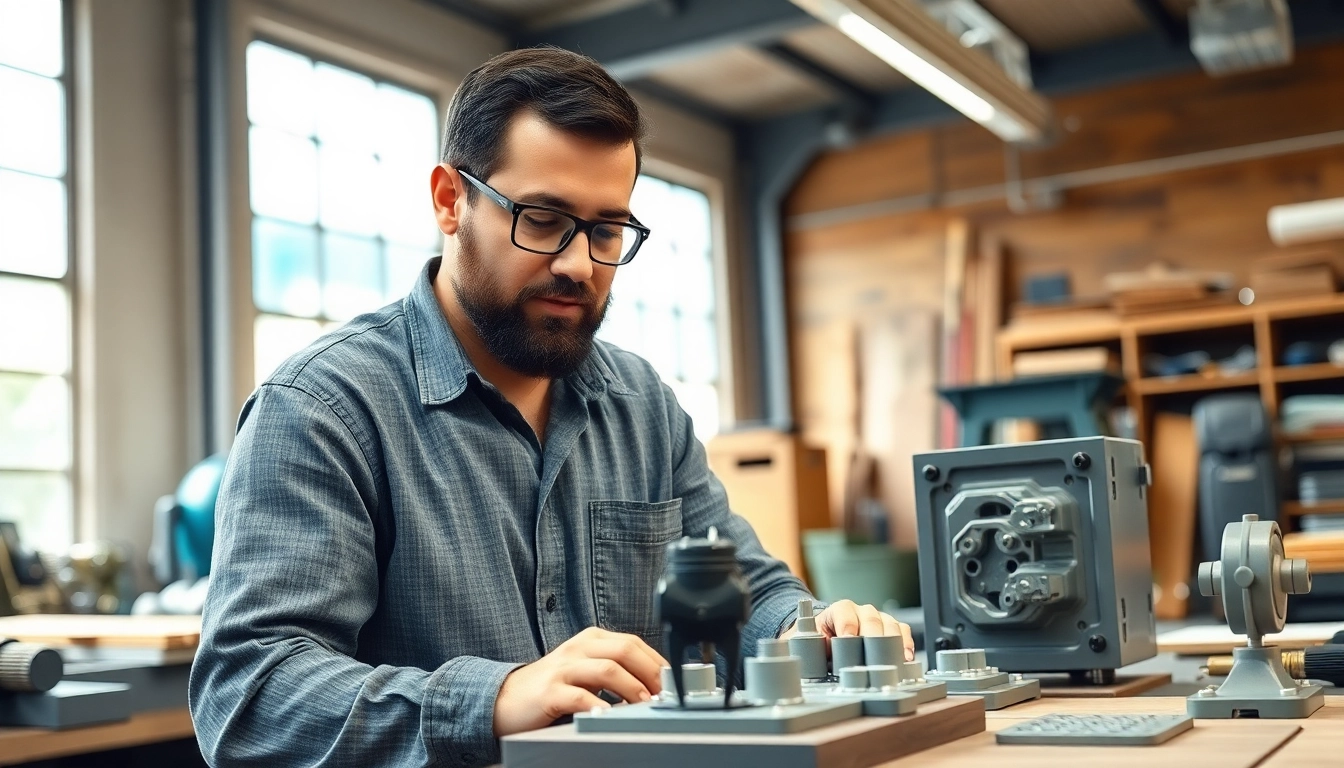
Understanding the Role of a Mold Maker for Injection Molding
In the world of manufacturing, the precision and quality of the molds used in plastic injection molding play a pivotal role in determining the success of the final product. A mold maker for injection molding is a skilled professional responsible for creating these intricate molds that must meet precise specifications. The importance of this role cannot be overstated, as the quality of the mold directly impacts production efficiency, product quality, and overall cost effectiveness.
What is a Mold Maker?
A mold maker is a specialist who fabricates molds used in injecting molten material, often plastic, into a pre-defined shape. These molds are vital in industries ranging from automotive to consumer goods. Mold makers work closely with engineers and designers to translate product specifications into functional molds. Their tasks often involve the design, machining, assembly, and testing of molds, ensuring that they function flawlessly before entering production.
Key Skills Required for Mold Makers
Mold making is a highly technical field that requires a combination of skills and attributes, including:
- Technical Proficiency: A solid understanding of machining processes, including CNC machining and electrical discharge machining (EDM), is crucial.
- Attention to Detail: Precision is key in mold making, as even the slightest error can lead to production faults.
- Problem-Solving Skills: Mold makers must be able to troubleshoot issues that arise during the manufacturing process.
- Computer-Aided Design (CAD) Skills: Familiarity with CAD software is essential for designing intricate molds.
- Project Management: Ability to manage timelines and coordinate with various teams ranging from design to production.
Importance of Quality in Mold Making
The quality of a mold is fundamentally tied to the efficiency of the production process. High-quality molds lead to:
- Increased Durability: Well-made molds last longer and can handle higher volumes of production without degradation.
- Enhanced Product Quality: Flawless molds yield high-quality components that meet or exceed specifications.
- Reduced Production Costs: Quality molds minimize defects and reduce waste, leading to cost savings in manufacturing.
How to Select a Mold Maker for Your Injection Molding Needs
Choosing the right mold maker can be a daunting task. Understanding the criteria that should drive your selection process is vital to ensuring your project’s success.
Criterias for Choosing a Mold Maker
When selecting a mold maker, consider the following criteria:
- Experience: Look for mold makers with a proven track record in producing molds for your specific industry.
- Technical Capabilities: Ensure they possess the modern machinery and technology needed to produce high-precision molds.
- Reputation: Check reviews and testimonials from previous clients to gauge their satisfaction with the mold maker’s services.
- Location: Proximity can matter for ease of communication and the potential for site visits during the mold design and testing phases.
Evaluating Experience and Expertise
Deep-dive into the background of potential mold makers. Assess their portfolio for diversity and complexity of molds they have created in the past. Check if they have worked on similar projects, and don’t hesitate to ask for references from previous clients. Engaging in discussions about your specific needs can also reveal the mold maker’s expertise and ability to meet your expectations.
Comparing Cost and Quality
Cost is always a consideration when selecting a mold maker, but quality should never be compromised. Get detailed quotes from multiple mold makers and ensure they provide insight into the materials and processes included in their pricing. Often, lower prices may indicate inferior quality or hidden costs later in the production phase. Therefore, maintaining a balance between cost-effectiveness and high-quality output is essential.
The Mold Making Process Explained
Understanding the process of how molds are made can help you appreciate the complexities involved and the expertise required from mold makers.
Step-by-Step Mold Creation Techniques
The mold-making process generally involves several key steps:
- Design Phase: Using CAD software, the mold maker creates a detailed blueprint of the mold based on product specifications.
- Material Selection: Selecting the appropriate materials for the mold, which is crucial for its durability and performance.
- Machining: Molds are machined using CNC or conventional machining processes to achieve the desired dimensions and surface finishes.
- Assembly: Once all parts are machined, the mold maker assembles them, ensuring all components fit perfectly together.
- Testing: Conducting tests with trial runs to verify the mold’s functionality and pinpoint any necessary adjustments.
Materials Used in Injection Molding
The selection of appropriate materials for mold creation is vital and typically includes:
- Steel: Commonly used for its strength and durability in high-volume production.
- Aluminum: It can be a cost-effective option for low to medium volume runs due to its lighter weight and good machinability.
- Plastics: Sometimes used for specialized applications or prototype molds.
Finishing Techniques for Quality Molds
Finishing touches can greatly enhance the mold’s functionality and longevity. Techniques include:
- Polishing: To ensure a smooth surface finish for reduced friction during the injection process.
- Coating: Applying surface treatments to improve temperature resistance and mold release properties.
- Testing and Adjustments: Final adjustments are made after initial testing to ensure optimal performance in production.
Common Challenges in Injection Mold Making
Even experienced mold makers face challenges throughout the mold-making process. Understanding and addressing these challenges is key to ensuring success.
Addressing Design Flaws
Design flaws can emerge during the early stages of mold development. Regular reviews, prototyping, and the implementation of design for manufacturability principles can help identify and rectify these challenges before they escalate.
Balancing Cost and Efficiency
When working with budgets, finding the sweet spot between cost and efficiency can be challenging. One approach is to invest more in the design and prototyping phases, which can pay off by reducing production costs and waste during the manufacturing phase.
Maintaining Consistency in Production
Variation in production quality can arise from numerous minor faults. Implementing strict quality control measures and regular maintenance schedules for equipment can mitigate these issues significantly.
The Future of Mold Making in Injection Molding
The industry is constantly evolving, driven by technological advancements and changing market demands. Staying ahead of these trends is essential for mold makers.
Innovations and Trends in the Industry
Emerging technologies like 3D printing, automation, and advanced software are changing the landscape of mold making. These innovations not only improve precision but also reduce lead times and costs associated with traditional manufacturing processes.
Impact of Technology on Mold Making
Technology has enhanced mold design and production techniques, leading to:
- Increased Efficiency: Automation in production reduces human error and increases output.
- Improved Communication: Software tools facilitate better collaboration between design and production teams.
- Enhanced Prototyping: Rapid prototyping allows for quick iterations and adjustments before final mold creation.
Preparing for the Next Generation of Mold Makers
The future of mold making rests heavily on continuous education and training. Emphasizing STEM education and vocational training programs can foster a new generation of skilled mold makers who are adept at using advanced technologies and processes.