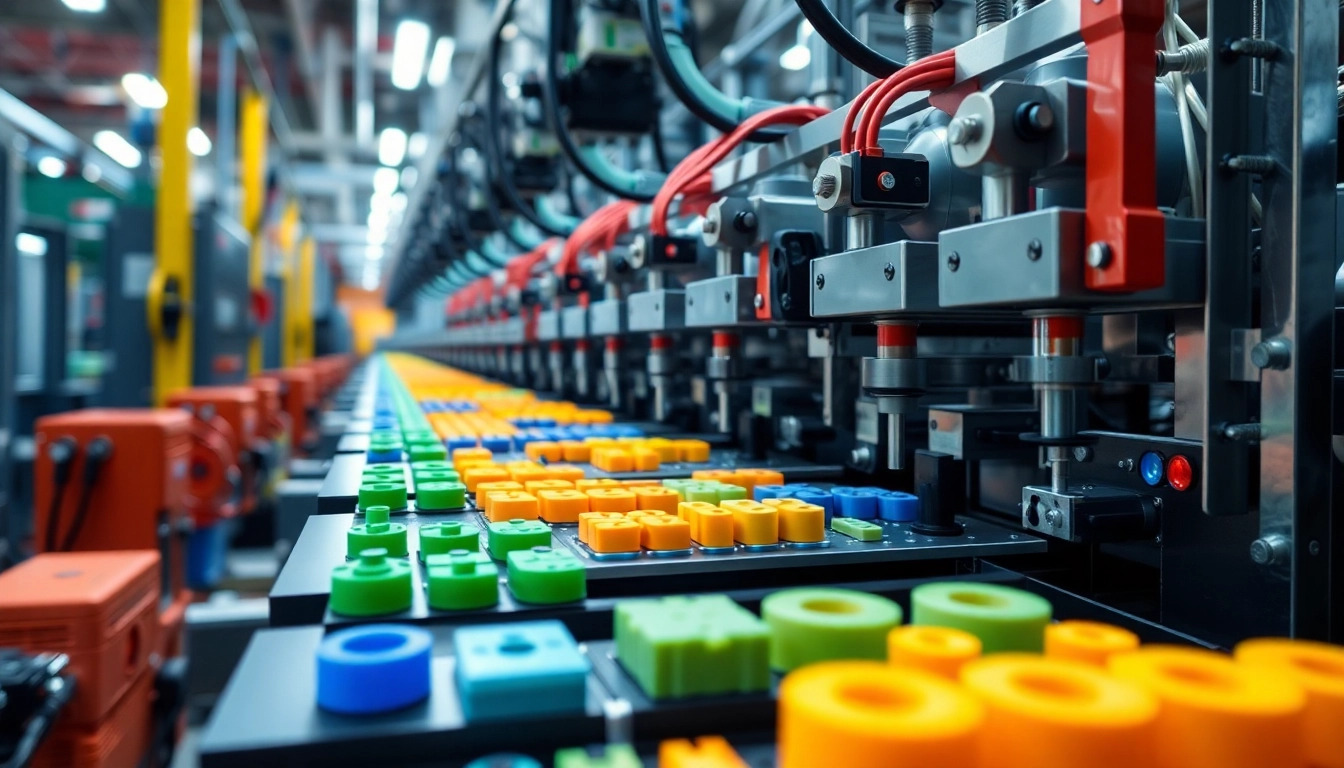
Understanding Injection Molded Parts
Injection molded parts are crucial in various manufacturing processes, playing an essential role in producing high-quality plastic components at scale. These parts are created through a method known as injection molding, where heated plastic is forced into a mold, cooling and solidifying to form precise shapes. This technique allows manufacturers to create complex geometries and intricate designs that meet specific needs across numerous industries. As this technique evolves, understanding the ins and outs of injection molded parts becomes increasingly important.
What Are Injection Molded Parts?
Injection molded parts are products manufactured using the injection molding process. This technique involves two key components: the molten plastic and the mold itself. The process consists of heating plastic to a liquid state, injecting it into a solid mold, and then allowing it to cool and harden into the desired shape. These parts are acclaimed for their uniform quality, scalability, and ability to produce both prototypes and final products efficiently.
The range of products made through injection molding is vast, including everyday items like containers, automotive components, and consumer electronics. The advantages of injection molded parts lie in their precision, repeatability, and the flexibility to utilize various materials, making them a go-to in modern manufacturing.
The Injection Molding Process Explained
The injection molding process unfolds in several critical stages:
- Material Preparation: The raw plastic is fed into a hopper, where it is heated and homogenized to achieve a consistent liquid state.
- Injection: The molten plastic is injected into a mold under high pressure, filling it completely to ensure the precise shape is captured.
- Cooling: The injected plastic cools and solidifies within the mold, typically within seconds to a few minutes, depending on the material and part thickness.
- Ejection: Once cooled, the mold opens, and ejector pins push the finished part out of the mold cavity.
This cycle can be repeated rapidly, allowing manufacturers to achieve substantial output with high precision. Modern technologies have introduced variations, such as multi-shot molding and insert molding, catering to more complex designs.
Materials Used in Injection Molded Parts
Choosing the right material is pivotal in the injection molding process. Common materials include:
- Thermoplastics: Materials like polyethylene (PE), polypropylene (PP), and polystyrene (PS) are well-known for their versatility and ease of processing.
- Thermosetting Plastics: These are polymers that, once set, cannot be remolded. Examples include epoxy and phenolic resins.
- Elastomers: Flexible materials such as rubber can be injected to produce compliant parts and products.
The choice of material influences not only the performance and longevity of the final product but also the feasibility and efficiency of the injection molding process itself.
Designing for Injection Molded Parts
The success of injection molded parts isn’t solely determined by the manufacturing process but also heavily reliant on design. Proper design considerations can significantly impact production efficiency, part quality, and material usage.
Best Practices for Design Considerations
Implementing best practices in design can enhance manufacturability and reduce costs:
- Draft Angles: Adding a slight draft angle facilitates easy ejection from the mold, preventing damage to the parts.
- Wall Thickness: Maintaining uniform wall thickness helps minimize warping and ensures consistent cooling throughout the part.
- Radii and Fillets: Incorporating rounded edges helps distribute stress evenly and reduces production issues like cracking.
- Feature Alignment: Aligning features along the tool’s split line minimizes complexity and enhances the part’s strength.
The Importance of Prototyping
Prototyping serves as a critical step in the injection molding design process. Early-stage prototypes allow designers to validate concepts, measure performance, and identify potential design flaws before final production. This step can save both time and money, allowing companies to refine their designs iteratively.
Using technologies such as 3D printing, manufacturers can create rapid prototypes to test form, fit, and function, enabling them to make educated decisions regarding the final designs.
Tips for Optimizing Molding Designs
Optimizing designs for injection molded parts involves evaluating performance, manufacturability, and economic feasibility. Key tips include:
- Collaborate Early: Engage with mold makers and production specialists during the design phase for insights on manufacturability.
- Simplify Assemblies: Whenever possible, design parts that can be produced as single, integrated components instead of multiple pieces.
- Utilize Simulation Software: Leverage advanced software to simulate the injection molding process, helping predict potential defects like sink marks or voids.
Applications of Injection Molded Parts
Injection molded parts find use in a wide array of industries, reflecting the versatility of the process. Understanding these applications can provide insights into the importance and impact of molded parts.
Common Industries Utilizing Injection Molding
Numerous industries incorporate injection molding, including:
- Automotive: From dashboard components to exterior trim, injection molded parts are integral in vehicle manufacturing.
- Consumer Electronics: Mobile phone cases, laptop components, and various electronic housings are often produced using injection molding techniques.
- Medical Devices: The need for precision and reliability in medical equipment makes injection molding a favored choice in healthcare.
- Home Goods: Everyday items such as storage containers, kitchenware, and plastic furniture are commonly injection molded for increased efficiency and cost-effectiveness.
Everyday Products Made from Injection Molded Parts
The ubiquity of injection molded products is evident in nearly every household. Some common examples include:
- Plastic bottles and caps
- Toys including Lego bricks
- Consumer appliances like blenders and mixers
- Automotive parts such as bumpers and dashboards
Custom Solutions for Specific Needs
One of the standout features of injection molding is the capability to create custom solutions tailored to specific requirements. Whether it’s through modifying existing molds or designing entirely new molds, manufacturers can meet a variety of demands. Customization allows businesses to target niche markets, differentiate their products from competitors, and achieve optimal performance for specialized applications.
Challenges in Injection Molding
Despite its advantages, the injection molding process is not without challenges. Understanding these challenges and their corresponding solutions is crucial for achieving seamless production.
Identifying Common Issues in Production
Manufacturers may encounter several issues during injection molding, including:
- Flash: This occurs when excess plastic seeps out of the mold, leading to undesirable edges.
- Short Shots: Parts that fail to fill completely can result from insufficient material or flow issues.
- Warpage: Uneven cooling can lead to distortion in parts, affecting their functionality and aesthetics.
Solutions to Overcome Injection Molding Challenges
By implementing targeted strategies, manufacturers can address common challenges, such as:
- Adjusting Mold Design: Modifying the mold architecture can help manage material flow, reducing flash and short shots.
- Temperature Control: Ensuring consistent temperature during the injection and cooling phases can mitigate warpage.
- Material Selection: Utilizing materials with specific properties can enhance moldability and reduce defects.
The Role of Quality Control in Production
Quality control is paramount throughout the injection molding process. Regular inspections and testing methods, such as dimensional analysis and aesthetic evaluations, ensure that each part meets stringent quality standards. Implementing advanced technologies, like machine learning algorithms, can predict potential defects based on historical data, allowing for proactive quality management.
The Future of Injection Molded Parts
The injection molding industry is on the brink of significant advancements. With ongoing research and development, the future promises innovative approaches that enhance efficiency, sustainability, and capabilities.
Trends in Injection Molding Technology
Emerging technologies include:
- Additive Manufacturing: Integrating 3D printing with traditional injection molding for rapid tool creation and prototyping.
- Smart Injection Molding: Utilizing IoT devices and sensors to monitor and optimize the injection molding process in real-time.
- Advanced Materials: Exploring new composite materials to enhance part performance while reducing weight and costs.
Innovations Impacting Injection Molded Parts
New innovations, including bio-based plastics and better recycling processes, aim to reduce waste and increase sustainability. The development of multifunctional materials that can endure varying conditions while maintaining performance broadens application possibilities for injection molded parts.
Environmentally Friendly Practices in Molding
The industry is increasingly shifting towards environmentally friendly practices, focusing on:
- Using Recycled Materials: Incorporating recycled plastics into the injection molding mix to decrease reliance on virgin materials.
- Reducing Waste: Implementing lean manufacturing techniques to minimize byproducts and excess material during the molding process.
- Energy Efficiency: Investing in energy-efficient machinery and processes to lower carbon footprints while maintaining high output.
As the landscape of manufacturing evolves, injection molded parts remain a foundational element, adapting to new technologies and user demands. With continuous innovation and a commitment to quality, the industry will foster sustainability and responsiveness, catering to an ever-changing marketplace.