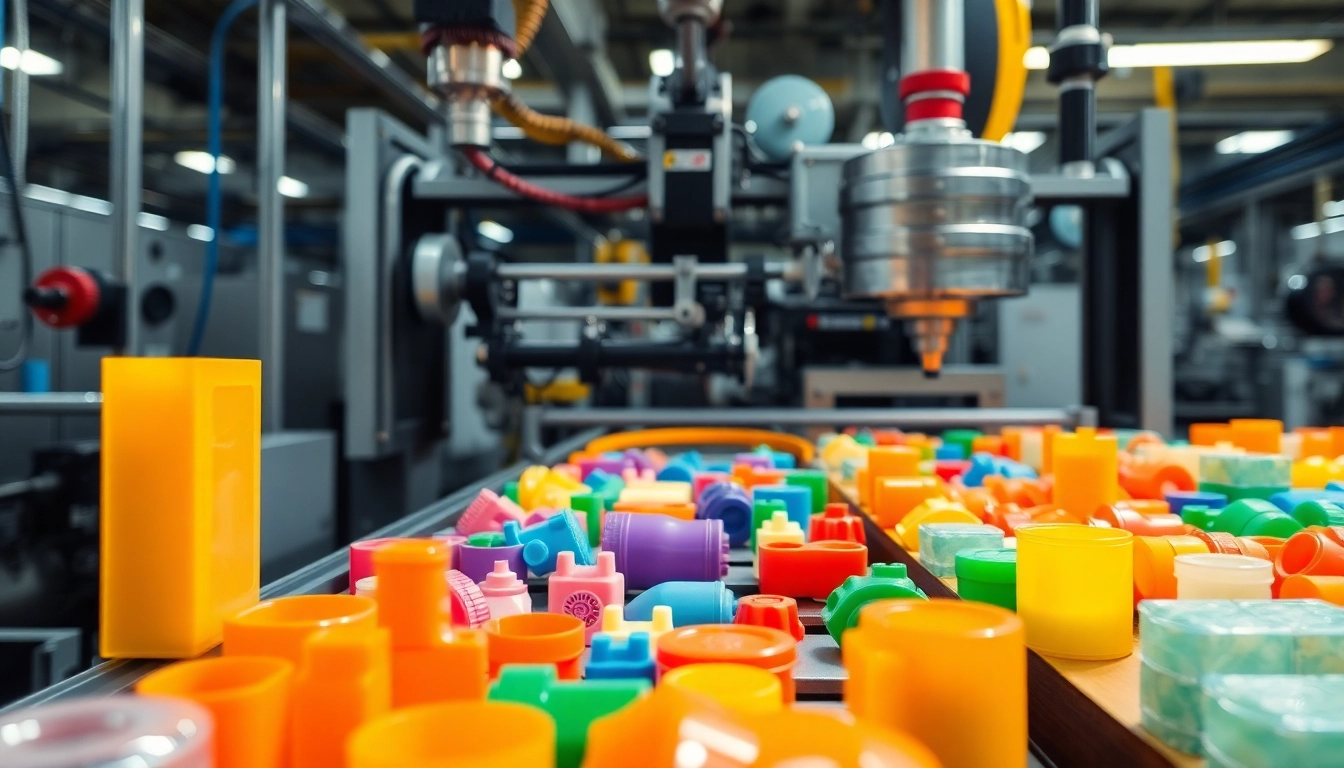
Understanding the Manufacture of Plastic Parts
The manufacture of plastic parts represents a fundamental process that is integral to modern product development and production. From automotive to consumer products, the versatility of plastics enables manufacturers to create a wide array of components that are both functional and aesthetically pleasing. As we delve into the methodologies behind plastic manufacturing, we will explore various techniques, materials, advantages, and the future of this essential industry.
Overview of Plastic Manufacturing Techniques
Plastic manufacturing encompasses several techniques, each serving specific application needs. The most prominent processes include injection molding, extrusion, and 3D printing. Understanding each technique through its process flow, materials used, and typical applications is key to selecting the most appropriate method for a project.
Common Materials Used in Production
The family of plastics is diverse, spanning thermoplastics, thermosets, and elastomers. Common materials include:
- Polyethylene (PE): Widely used due to its low cost and versatility.
- Polypropylene (PP): Known for its strength and lightweight properties, often used in packaging.
- Polyvinyl Chloride (PVC): Frequently utilized in construction and healthcare for its durability.
- Polystyrene (PS): Common in consumer products and packaging.
- Acrylonitrile Butadiene Styrene (ABS): Popular in electronics and automotive for its toughness and impact resistance.
Key Advantages of Plastic Parts Manufacturing
Manufacturing plastic parts provides numerous benefits that contribute fundamentally to their widespread adoption:
- Cost-Effectiveness: Plastic parts can be produced at lower costs compared to metal or glass components.
- Lightweight: Reducing the weight of products enhances usability and shipping efficiencies.
- Design Flexibility: The ability to create complex shapes and intricate designs that might be impossible with other materials.
- Corrosion Resistance: Plastics do not rust or corrode like metals, contributing to longer life cycles and reduced maintenance.
- Sustainability Potential: Many plastics can be recycled, and developments in bioplastics are paving the way for greener alternatives.
Popular Methods in the Manufacture of Plastic Parts
Injection Molding: The Gold Standard
Injection molding stands as the leading technique in plastic manufacturing, ideal for high-volume production. The process involves melting plastic pellets, injecting the molten plastic into a mold under high pressure, and allowing it to cool and solidify. This method is favored for its ability to produce parts with intricate geometries and smooth finishes consistently. It’s particularly suited to manufacturing critical components in industries such as automotive, electronics, and consumer goods.
Extrusion and Its Applications
Extrusion involves feeding plastic into a heated chamber, where it is melted and forced through a die, shaping it into continuous lengths such as tubes or sheets. It is commonly used for applications like pipes, insulation for electrical cables, and film for packaging. One key advantage of extrusion is versatility; manufacturers can create various cross-sectional shapes without significant re-tooling.
3D Printing’s Role in Modern Manufacturing
Emerging technologies, particularly 3D printing, are revolutionizing plastic part manufacturing. This additive manufacturing process allows for the layer-by-layer creation of parts directly from digital models. While it traditionally served prototyping needs, its applications have expanded to include manufacturing end-use parts, particularly in custom orders and low-volume production where design flexibility is prioritized.
Choosing the Right Process for Your Project
Factors Influencing Manufacturing Decisions
When selecting a plastic manufacturing process, several factors must be considered:
- Volume: The required quantity greatly influences the process. High volumes typically favor injection molding, while low volumes may benefit from 3D printing.
- Material Properties: The characteristics of the plastic selected dictate the manufacturing method. Certain processes work better with specific types of polymers.
- Complexity of Design: Products with intricate designs may necessitate more advanced manufacturing techniques like injection molding or 3D printing.
- Cost Considerations: Analyzing production costs, including tooling, setup, and material costs, is crucial for budget compliance.
Cost Comparison of Different Techniques
Understanding the cost implications of different manufacturing techniques is fundamental for decision-making:
- Injection Molding: Higher upfront costs for tooling but lower cost per unit when producing large quantities.
- Extrusion: Generally lower setup costs; ideal for continuous shapes, yet the material must be compatible.
- 3D Printing: Higher cost per unit but no need for tooling allows for economical production in low volumes and prototypes.
Sample Use Cases and Examples
Practical examples demonstrate how the choice of manufacturing process impacts project outcomes:
- Consumer Electronics: High-volume production of cases and components often relies on injection molding for precision and consistency.
- Automotive Industry: Complex parts like dashboards are frequently made using injection molding due to their intricate designs and requirements for durability.
- Custom Prototyping: Startups often use 3D printing to develop prototypes quickly before committing to large-scale manufacturing.
Quality Control in Plastic Part Production
Essential Testing Procedures
Quality assurance is a non-negotiable element of plastic part manufacturing. Testing procedures ensure that the final product meets specified standards, including:
- Dimensional Accuracy: Verify that the dimensions and tolerances align with specifications.
- Mechanical Properties Testing: Assess strength, flexibility, and durability through standardized tests such as tensile or impact tests.
- Visual Inspection: Examine surface finish and the overall integrity of parts for defects.
Common Defects and Solutions
Recognizing and addressing common manufacturing defects is vital for maintaining product quality:
- Warpage: Often arises from uneven cooling; solutions include adjusting mold temperatures and using better cooling methods.
- Bubbles or Voids: Can occur during the injection process; implementing better material handling and venting processes can mitigate this issue.
- Scratches and Surface Defects: Proper handling and choosing the right materials can help reduce surface imperfections.
Importance of Certifications and Standards
Adherence to industry standards and obtaining necessary certifications ensures that products are of the highest quality, ascertaining user safety and regulatory compliance. Examples include ISO certifications and specific material safety standards pertinent to industries such as food packaging and medical devices.
Future Trends in Plastic Parts Manufacturing
Innovations in Sustainable Practices
As consumers become more environmentally conscious, the plastics industry is witnessing a shift towards sustainability. Innovations include:
- Bioplastics: Derived from renewable sources, these materials aim to reduce dependency on fossil fuels.
- Recycling Technologies: Advances in chemical recycling offer improved options for re-processing post-consumer plastics back into raw materials.
Advancements in Technology and Automation
Technological advancements such as smart manufacturing and Industry 4.0 are transforming plastic part production. This includes:
- Automation: Reduces labor costs and enhances consistency in production.
- IoT Integration: Utilizing sensors and data analytics for real-time monitoring and predictive maintenance of machines.
Market Predictions for the Plastic Industry
The future of the plastic manufacturing industry is exceedingly bright, with predictions indicating steady growth driven by demand in various sectors including automotive, aerospace, and consumer goods. Here, the emphasis will likely be on innovation, sustainability, and technological advancements that streamline processes and improve product quality.