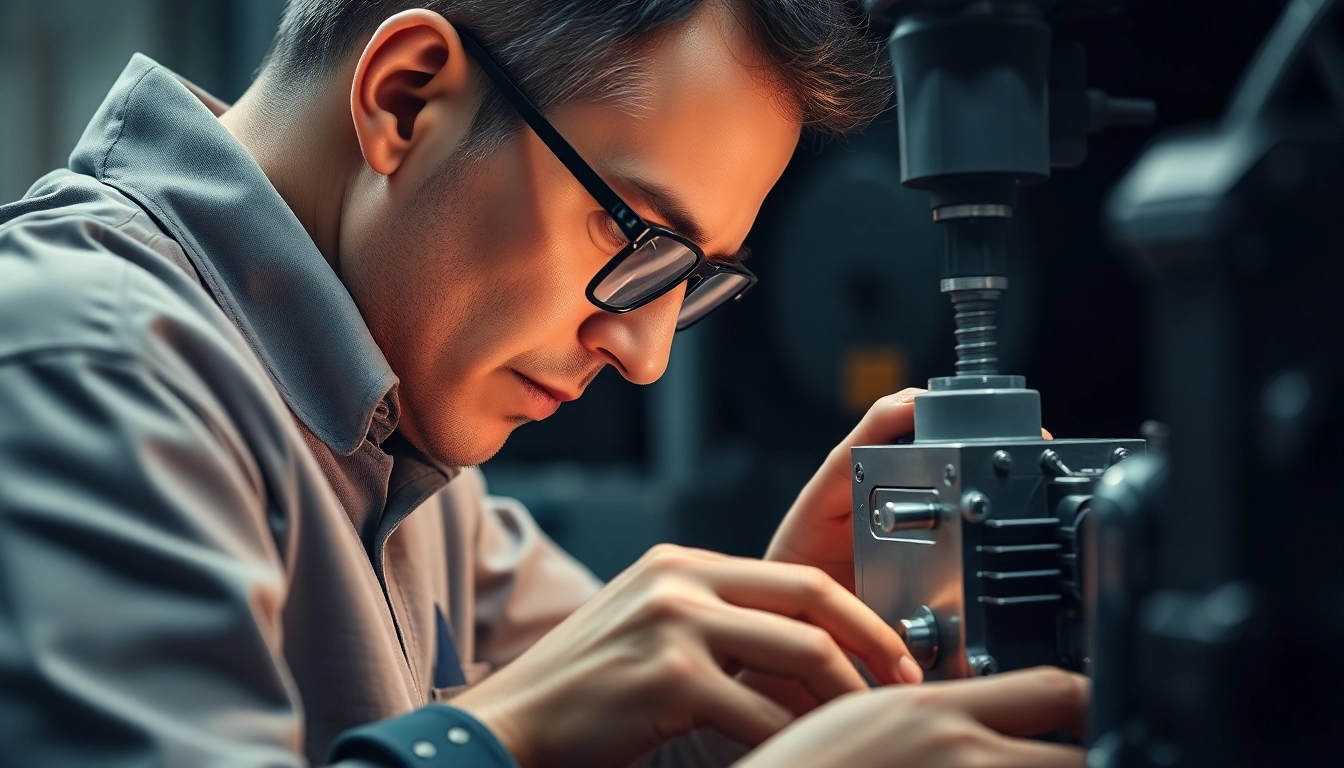
Understanding Injection Molding and Its Importance
Injection molding is a pivotal manufacturing process that plays a significant role in producing complex shapes and high-volume plastic parts. As industries increasingly rely on plastic components for diverse applications, the demand for skilled mold makers for injection molding continues to rise. Understanding the fundamental aspects of injection molding and the expertise of mold makers helps businesses optimize production efficiency and lower manufacturing costs.
The Role of Mold Makers in Injection Molding
Mold makers are integral to the injection molding process. They are responsible for designing and creating molds that shape the molten plastic into its final form. This process requires high precision because even the slightest deviation in mold design can lead to defects in the finished product. Mold makers utilize a range of tools and technologies, including computer-aided design (CAD) software and computer numerical control (CNC) machining, to create molds that meet stringent specifications.
In addition to the technical skill set, mold makers also need to understand materials science, as the choice of material used in the mold affects its durability, the quality of the molded parts, and overall manufacturing costs. High-quality molds lead to consistent output, better product quality, and reduced waste during the production process.
Applications of Injection Molding in Various Industries
Injection molding finds applications across numerous sectors, including automotive, consumer goods, electronics, and medical devices. In the automotive industry, molded parts such as dashboard components, bumpers, and intricate interior fittings are produced efficiently using this method. The consumer goods sector leverages injection molding to manufacture items ranging from toys to kitchenware, ensuring affordability and uniformity in design.
In electronics, components like housings and connectors are fabricated via injection molding, which allows for precision engineering and mass production. The medical industry benefits as well, producing syringes, surgical instruments, and other critical items that must meet high safety and performance standards.
Overall, the versatility of injection molding makes it a cornerstone of modern manufacturing, contributing to innovation and efficiency in product design and production.
Common Challenges in Mold Making
Despite its advantages, the injection molding process faces several challenges that can affect production outcomes. One common challenge is ensuring the mold’s longevity and quality. Molds can wear down over time, leading to defects in molded parts, such as surface imperfections and dimensional inaccuracies. To combat this, investment in high-quality materials and regular maintenance of molds are crucial.
Another significant issue is managing the cooling time of molds. Proper cooling is vital for preventing warping and ensuring that parts retain their designed shape. Overheating can result in surface defects, while cooling that is too rapid can lead to cracking. Mold makers must design molds with adequate cooling channels to optimize temperature management.
Finally, the cost associated with creating complex molds can be substantial. Mold makers must balance complexity with cost-efficiency, often using advanced simulation technologies to ensure that designs are optimized before manufacturing begins.
Key Qualities of an Ideal Mold Maker for Injection Molding
Choosing an ideal mold maker for injection molding is critical for a successful manufacturing process. Businesses should look for specific qualities that indicate a mold maker’s capability and reliability in delivering high-quality results.
Technical Expertise and Experience
An experienced mold maker possesses technical expertise in various aspects of mold design, materials, and manufacturing processes. The production of injection molds requires a high level of precision and understanding of machining techniques, such as CNC machining and electrical discharge machining (EDM).
Additionally, an experienced mold maker will not only have technical know-how but also hands-on experience working with different plastics and their behaviors during the injection molding process. This experience allows them to predict potential challenges and mitigate risks, ensuring a smoother production process.
Materials and Technology Used
The choice of materials and the technology employed to create molds significantly impacts the quality of the molded parts. A proficient mold maker will be well-versed in various materials like aluminum and steel, understanding which is most suitable for specific applications. High-quality molds typically require durable materials capable of withstanding the pressures and temperatures involved in the injection molding process.
Moreover, mold makers should stay updated with emerging technologies, such as 3D printing and advanced simulation software, to enhance mold design and production efficiency. Integrating modern technologies can streamline processes, reduce lead times, and improve overall output quality.
Customer Service and Communication Skills
Excellent customer service is a hallmark of a reliable mold maker. Effective communication throughout the project lifecycle enables clarity and addresses any concerns that may arise. A mold maker should be approachable and willing to collaborate with clients, providing updates and feedback as needed.
Transparency in pricing, timelines, and any potential challenges is essential for cultivating a successful partnership. A mold maker who prioritizes customer satisfaction will ultimately help in managing expectations and delivering results that align with client goals.
Evaluating Cost and Value in Mold Making Services
Understanding the costs associated with mold making and balancing that with the value provided is critical for any manufacturer. This involves a strategic evaluation of different factors influencing pricing and outcomes.
Understanding Pricing Models for Injection Mold Makers
Mold making costs can vary considerably depending on several factors, including complexity, material choice, and production volume. Common pricing models include fixed prices for standard molds and variable rates that depend on the custom requirements of a particular project.
Potential clients should seek detailed quotes that include factors like design time, machining costs, and material expenses. A thorough breakdown of costs enables manufacturers to make informed decisions about their mold-making options.
Cost vs. Quality: Making the Right Choice
While cost is an essential factor, it is vital to remember that cheaper is not always better. Investing in high-quality molds may require a higher upfront cost, but these molds can lead to greater efficiency, lower failure rates, and better-end product quality over time. When evaluating potential mold makers, manufacturers should consider their track record of delivering high-quality results versus their pricing structure.
Additionally, the long-term savings from reduced maintenance and downtime should be factored into the overall cost analysis. Organizations that opt for quality over cost can reap significant rewards in the long run.
Long-Term Value and Return on Investment
The ideal mold making decision should also consider long-term value. Manufacturers should analyze the potential return on investment (ROI) of engaging a particular mold maker. ROI can be calculated by assessing factors like expected lifespan of molds, anticipated production volume, and overall product reliability and performance.
Evaluating the long-term implications of mold quality on production efficiency and product quality can highlight how strategic investments will positively impact business outcomes over time.
Case Studies: Successful Collaborations with Mold Makers
Examining successful collaborations between manufacturers and mold makers provides valuable insights into best practices and effective strategies that can be replicated in other contexts.
Innovative Projects and Their Outcomes
Several companies have benefited from partnering with skilled mold makers to create innovative products. For example, a medical device manufacturer worked closely with a mold maker specializing in complex geometries to develop a new type of syringe. By leveraging advanced mold design techniques and a deep understanding of materials, they achieved a reduction in production costs while improving product reliability. This collaboration resulted in a significant increase in market share for the manufacturer.
Lessons Learned from Leading Mold Makers
Leading mold makers often share insights that help improve processes and foster innovation. One key lesson is the importance of iterative feedback loops between the mold maker and the client. Regular check-ins during the design and production phases help identify issues early, allowing for timely corrections and adaptation to changing requirements.
Another lesson involves investing in training and development for engineers and technicians. Continuous learning ensures that teams use the latest techniques and materials, optimizing the overall mold-making process.
Comparative Analysis of Different Providers
When evaluating various mold-making providers, conducting a comparative analysis is essential to understand differences in capabilities, pricing, and quality assurance processes. Manufacturers can look into testimonials, case studies, and industry certifications as part of their research. By benchmarking potential partners, organizations can select the best alignments with their specific needs and objectives.
Choosing a mold maker involves looking beyond mere pricing to assess experience, technical capability, and reliability. Evaluating these aspects ensures a solid partnership that yields high-quality outputs and innovative solutions.
Future Trends in Mold Making for Injection Molding
The field of mold making is constantly evolving, driven by technological advancements and changing market demands. Understanding emerging trends can help businesses prepare for the future of injection molding.
Emerging Technologies Impacting the Industry
Technological advancements such as additive manufacturing (3D printing) and advanced simulation tools are revolutionizing the mold-making process. 3D printing allows for rapid prototyping and the production of complex mold designs that traditional methods may not achieve. This technology enhances design flexibility and accelerates time-to-market for new products.
Simulation tools enable mold makers to analyze and optimize every phase of production, including material flow and cooling rates, ultimately leading to more efficient designs and better-quality products.
Sustainability Practices in Mold Making
As sustainability becomes a priority in manufacturing, mold makers are adapting practices to minimize their environmental impact. This includes using recycled materials in molds and optimizing designs to reduce waste during production. Manufacturers are increasingly seeking partners committed to environmentally responsible practices, making sustainability a crucial consideration for mold makers.
Additionally, advancements in materials science are giving rise to bio-based and biodegradable plastics, further aligning the injection molding process with sustainability goals.
The Future of Customization and Rapid Prototyping
As consumer demands evolve towards customization, mold makers are pressured to adapt quickly. The future will see more emphasis on rapid prototyping, allowing for faster iterations and fine-tuning of mold designs. With market trends leaning towards personalized products, understanding consumer preference is crucial, and mold makers who can deliver customized solutions efficiently will thrive.
Overall, being attuned to these emerging trends will equip manufacturers and mold makers alike to seize opportunities and overcome challenges in the evolving landscape of injection molding.