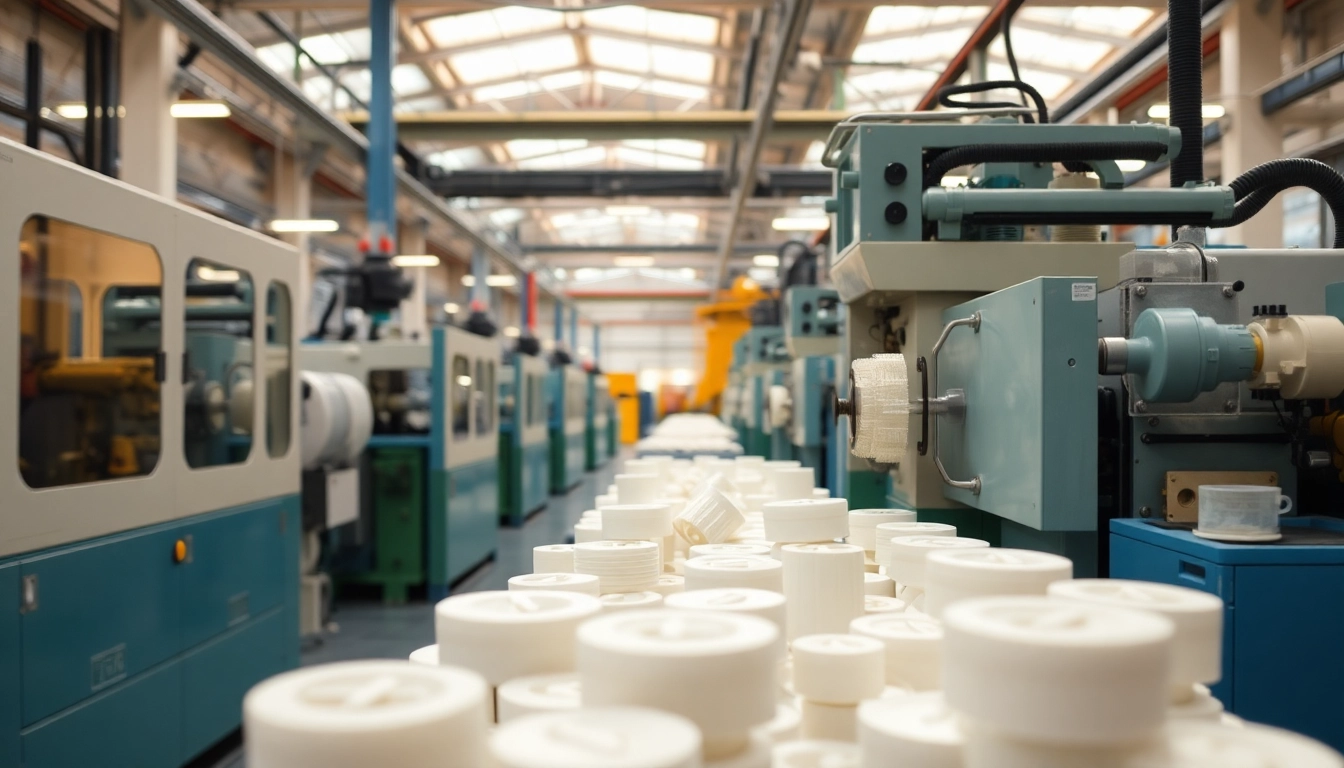
Understanding Blow Moulding: A Comprehensive Overview
Blow moulding is an innovative manufacturing process extensively utilized for creating hollow plastic parts. The versatility of blow moulded plastic parts allows for a wide range of applications across various industries, including consumer goods, automotive, and industrial sectors. In this section, we will delve into the fundamentals of blow moulding, examining what these plastic parts are, their common applications, and the distinct advantages they offer.
What Are Blow Moulded Plastic Parts?
Blow moulded plastic parts are products created through a manufacturing process that involves blowing air into molten plastic to form hollow objects. This technique is particularly efficient for producing items where a hollow shape is required, such as bottles, containers, and tanks. The process consists of several steps, including heating a plastic preform, inflating it within a mould, and allowing it to cool and harden into the desired shape. The end result is lightweight, durable, and often more cost-effective than other manufacturing methods, making it an essential technology in modern plastic manufacturing.
Common Applications of Blow Moulding
Blow moulding is utilized in a vast array of sectors due to its adaptability in creating various products. Some of the most common applications include:
- Beverage Bottles: One of the largest markets for blow moulded products, especially for soft drinks, water, and alcoholic beverages.
- Industrial Containers: Used for packaging chemicals, oils, and other industrial fluids, these containers are vital for transportation safety.
- Toys: Many plastic toys are produced using blow moulding, providing lightweight and durable options for children.
- Automotive Parts: Components such as fuel tanks and interior parts benefit from the lightweight and insulating properties of blow moulded plastics.
The Advantages of Using Blow Moulded Parts
There are several advantages to using blow moulded plastic parts, making them a preferred choice among manufacturers:
- Cost-Effectiveness: The blow moulding process is generally less expensive than injection moulding, especially for large volume production runs.
- Lightweight: Blow moulded products are typically lighter than their injection-moulded counterparts, making them easier to transport and handle.
- Design Flexibility: The blow moulding process allows for complex shapes and varied wall thicknesses, catering to diverse design needs.
- Rapid Production: The cycle times are shorter compared to many other manufacturing processes, enabling faster time to market for products.
The Blow Moulding Process: Step-by-Step Guide
The blow moulding process can be broken down into several steps to highlight how blow moulded plastic parts are made. Understanding this process is crucial for anyone involved in product design, manufacturing, or quality control.
Materials Used in Blow Moulding
Various plastics can be used in blow moulding, including:
- Polyethylene (PE): Widely used due to its strength and flexibility. Available in high-density (HDPE) and low-density (LDPE) variants, each suited for specific applications.
- Polypropylene (PP): Known for its toughness and fatigue resistance, making it ideal for products requiring durability.
- Polyethylene Terephthalate (PET): Commonly used for beverage bottles, PET offers excellent clarity and gas barrier properties.
- PVC: Generally used for products needing good chemical resistance.
Types of Blow Moulding Techniques
Various techniques are employed in blow moulding, allowing for different product characteristics:
- Extrusion Blow Moulding (EBM): Involves extruding a tube of molten plastic (parison) that is then inflated into a mould.
- Injection Blow Moulding (IBM): Combines injection moulding and blow moulding processes to create precise hollow products.
- Injection Stretch Blow Moulding (ISBM): Involves stretching the parison before blowing, enhancing the strength and clarity of the final product, commonly used in high-end beverage bottles.
Understanding Production Cycle Times
Production cycle times can vary significantly depending on the blow moulding technique used:
- EBM: Typically shorter cycle times due to the simultaneous production of multiple parts.
- IBM: Takes more time than EBM but offers higher precision and quality.
- ISBM: Cycle times can be longer, but the advantage lies in the material properties achieved.
Best Practices in Designing Blow Moulded Parts
Designing efficient and effective blow moulded parts requires careful consideration to minimize production issues and enhance product performance. Here are some best practices:
Considerations for Mold Design
Effective mould design plays a vital role in the blow moulding process. Key considerations include:
- Wall Thickness: Consistency in wall thickness helps prevent weak points and ensures even cooling.
- Mould Temperature: Maintaining optimal mould temperature can reduce cycle times and improve surface quality.
- Ventilation: Proper venting is crucial to allow air to escape and prevent defects during the blowing process.
Common Design Flaws and Solutions
Addressing common design flaws can significantly improve the outcome of blow moulded parts:
- Inconsistent Wall Thickness: Solution: Use techniques such as finite element analysis (FEA) during the design phase to ensure uniform thickness.
- Surface Imperfections: Solution: Improve mould surface finish and control cooling rates to minimize defects.
- Weak Points: Solution: Optimize the design to avoid sharp corners or sudden changes in geometry that can compromise strength.
Enhancing Aesthetic Quality in Blow Moulding
To enhance the aesthetic qualities of blow moulded parts, manufacturers can employ various techniques:
- Color and Texture: Incorporating additives or changing the surface finish can provide desired color and texture to products.
- Labeling and Printing: Advances in printing technology enable high-quality graphics and branding directly on blow moulded surfaces.
- Custom Moulds: Investing in custom moulds can yield unique shapes and features that improve the product’s market appeal.
Choosing the Right Supplier for Blow Moulded Parts
Selecting the appropriate supplier for blow moulded parts is crucial for ensuring quality and reliability. The following are key factors to consider during the selection process:
Evaluating Supplier Credentials
Before partnering with a supplier, it’s essential to verify their credentials:
- Certifications: Look for suppliers with relevant certifications, such as ISO 9001 for quality management and ISO 14001 for environmental management.
- Experience: Evaluate the supplier’s experience in your industry to ensure they understand your specific needs.
- References: Request references or case studies to gauge the reliability and quality of their previous work.
Understanding Pricing Models
The pricing structure of blow moulded parts can vary widely, and understanding this can help manage expectations:
- Cost per Part: Recognize how factors such as design complexity and material choices influence unit pricing.
- Volume Discounts: Many suppliers offer discounts for bulk orders, which can significantly lower the overall cost.
- Additional Services: Understand if the supplier provides additional services, such as logistics or assembly, which may impact pricing.
Supplier Relationship Management
Building a successful relationship with your supplier is essential for long-term success. Key strategies include:
- Regular Communication: Maintain open lines of communication to quickly address issues and adapt to changing needs.
- Performance Reviews: Conduct periodic reviews to assess supplier performance against agreed-upon metrics.
- Collaboration: Work together on product development to leverage combined expertise for improved outcomes.
Future Trends in Blow Moulding
The blow moulding industry is continuously evolving, driven by technological advancements and changing market demands. Here are some future trends to consider:
Innovations in Material Science
The development of new materials and formulations can enhance the functionality and sustainability of blow moulded products:
- Biodegradable Plastics: Increasing interest in sustainable materials will lead to the adoption of biodegradable resins suitable for blow moulding.
- Recyclable Materials: The use of recyclable plastics will gain traction, aligning with global sustainability initiatives and reducing environmental impact.
Advancements in Blow Moulding Machinery
Technological improvements in blow moulding machinery will enhance production capabilities:
- Automation: The integration of automation technologies can streamline processes, increase efficiency, and reduce labor costs.
- IoT Integration: Smart manufacturing practices will enable real-time monitoring and data analysis, leading to improved quality control.
Environmental Considerations and Sustainability
Environmental sustainability is becoming increasingly important in the blow moulding industry:
- Energy Efficiency: Suppliers will be pressured to adopt energy-efficient processes that lower energy consumption and reduce carbon footprints.
- Waste Reduction: Innovations that minimize waste during the manufacturing process will be prioritized to reduce overall environmental impact.