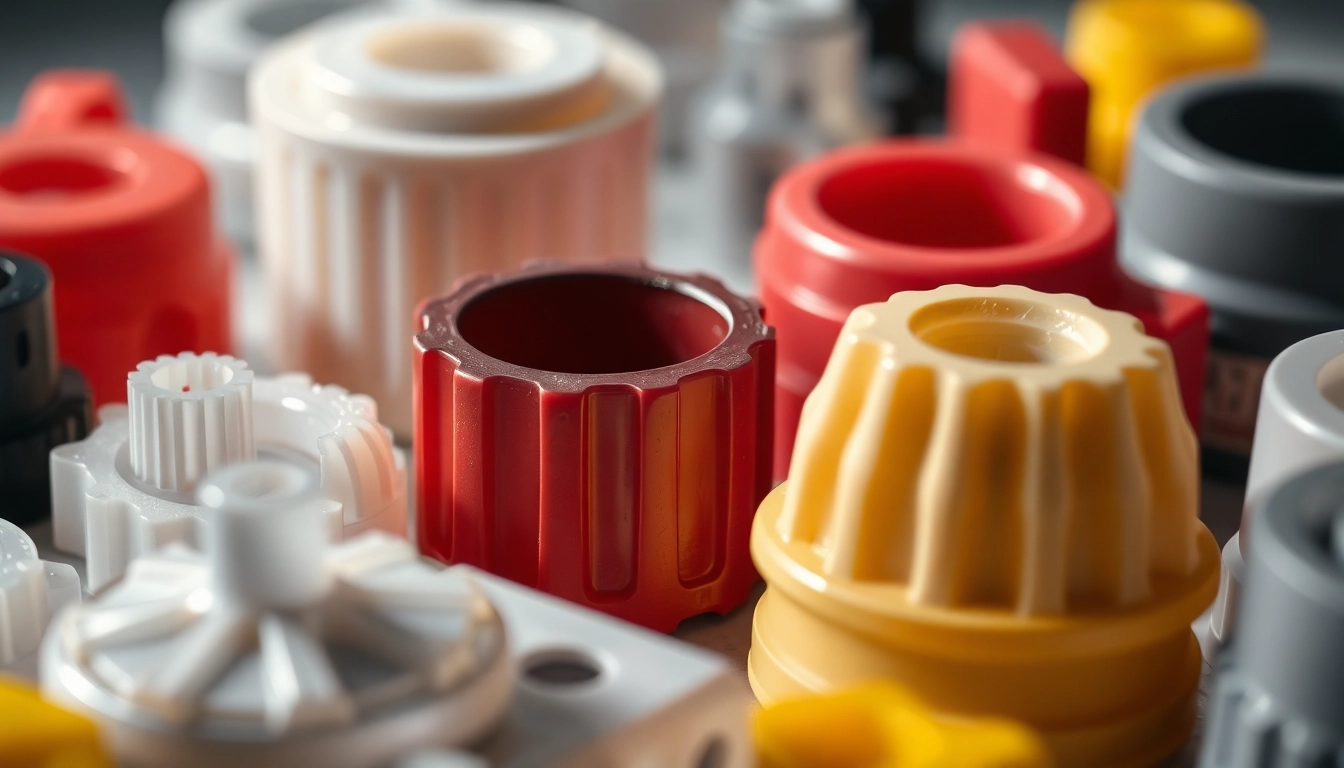
Introduction to Blow Moulded Plastic Parts
Blow moulded plastic parts are integral components in countless applications ranging from consumer goods to industrial equipment. This innovative manufacturing process allows for the creation of hollow plastic shapes with precision and efficiency. Understanding the intricacies of blow moulding not only highlights its significance in modern manufacturing but also empowers businesses to make informed decisions when sourcing these parts. By leveraging this knowledge, companies can enhance their product offerings and streamline production operations. For those interested in exploring the manufacturing process, blow moulded plastic parts represent a versatile solution in the world of plastic fabrication.
What Are Blow Moulded Plastic Parts?
Blow moulded plastic parts are hollow components created through a specialized industrial process known as blow moulding. This technique involves inflating a heated plastic material within a closed mould to achieve the desired shape. Products manufactured using this method typically include bottles, containers, and various custom shapes utilized across multiple sectors such as automotive, food, and consumer products.
The Blow Moulding Process Explained
The blow moulding process generally involves three core stages: preform preparation, moulding, and cooling. Initially, a plastic resin is heated until sufficiently malleable. This plastic is then formed into a “parison,” which resembles a hollow tube. The parison is placed into a mould, and compressed air is injected, causing the molten plastic to expand and fill the cavity of the mould. After the mould takes shape, the plastic is cooled and solidifies, producing a final product that is ready for ejection. This method grants exceptional repeatability and precision, making it highly suitable for mass production.
Common Uses in Various Industries
Blow moulding is widely employed across an array of industries. The beverage industry relies heavily on blow-moulded bottles, while the automotive sector utilizes blow-moulded parts for components like air ducts and fuel tanks. Moreover, household items such as toys and storage containers often benefit from this manufacturing process due to its efficiency and cost-effectiveness. As industries adopt more innovative designs, the applications of blow moulded plastic parts continue to expand, underscoring their versatility and importance.
Types of Blow Moulding Techniques
Extrusion Blow Moulding
Extrusion blow moulding is one of the most common methods for creating hollow plastic parts. In this technique, the parison is extruded from a die and then transferred into a mould. The process is particularly suitable for producing items with a uniform wall thickness and is widely used for manufacturing bottles and large containers. Its strengths lie in its speed and cost-effectiveness for high-volume production, but it may have limitations when it comes to complex geometries.
Injection Blow Moulding
Injection blow moulding combines both injection and blow moulding processes. Initially, a preform is created through injection moulding, and then it is transferred to a blow mould where air expands the preform to the desired shape. This technique is particularly useful for creating precise and complex parts, such as narrow-necked bottles, where tolerances are critical. Due to the two-step process, injection blow moulding can be slightly more expensive but offers high-quality results.
Injection Stretch Blow Moulding
This advanced technique of blow moulding involves stretching the preform prior to inflating it within the mould. This stretching results in enhanced strength and clarity of the final product, making it ideal for applications requiring higher durability and cosmetic appeal. Frequently utilized in the production of PET bottles for beverages, injection stretch blow moulding allows for better material distribution and weight optimization, which can be crucial for sustainability efforts.
Materials Used in Blow Moulding
Common Plastics for Blow Moulding
The most prevalent materials used in blow moulding include:
- Polyethylene (PE) – Available in several forms, including High-Density Polyethylene (HDPE) and Low-Density Polyethylene (LDPE), PE is known for its strength and resistance to chemicals.
- Polypropylene (PP) – This material offers excellent fatigue resistance and is often used in automotive applications.
- Polyethylene Terephthalate (PET) – PET is particularly beneficial for beverage containers, offering excellent clarity and barrier properties.
- Polyvinyl Chloride (PVC) – Known for its versatility, PVC is commonly used in construction and plumbing applications.
Benefits and Drawbacks of Each Material
Each material comes with its unique set of advantages and disadvantages. For instance, while polyethylene is cost-effective and durable, it may not withstand high temperatures. PET, while excellent for clarity and chemical resistance, often comes at a higher cost, making it less desirable for budget-sensitive applications. Understanding these trade-offs allows manufacturers to select the most suitable material for their specific needs, maximizing performance while minimizing costs.
Recycling and Sustainability Considerations
With growing concerns over plastic waste, the recycling of blow moulded products is becoming an essential consideration for manufacturers. Many blow-moulded items, particularly those made from PET, are recyclable and can be reprocessed into new products. The industry is also moving towards using recycled materials in the production of new blow moulded parts, promoting sustainability and reducing the environmental impact. Exploring these options not only meets consumer expectations but may also result in cost savings over time.
Applications of Blow Moulded Plastic Parts
Consumer Goods
The consumer goods sector is arguably one of the largest users of blow moulded parts. From shampoo bottles to food containers, the appealing aesthetics and practical functionality of blow moulded items make them a popular choice. Their lightweight and durable nature also aligns well with consumer preferences for convenience and ease of use.
Industrial Equipment
In industrial applications, blow moulded components are utilized for manufacturing tanks, ducting systems, and custom housings that require lightweight yet sturdy properties. The process allows for intricate designs that meet specific requirements often found in various industries, enhancing operational efficiency. Customisation possibilities can lead to significant advantages in terms of design flexibility and innovation.
Automotive Components
The automotive industry benefits greatly from blow moulded parts, using them for fuel tanks, air ducts, and various plastic covers. The ability to produce complex shapes while ensuring high structural integrity is vital for modern automotive design. Additionally, the lightweight nature of blow moulded components contributes to overall fuel efficiency, an essential consideration in today’s environmentally conscious market.
Choosing the Right Manufacturer for Blow Moulded Parts
Key Considerations for Selection
Selecting a reliable manufacturer for blow moulded parts requires careful evaluation. Key factors to consider include the manufacturer’s experience and expertise, the range of materials they can work with, and their capabilities in ensuring precision and quality. Additionally, verifying their compliance with industry standards can help assure you of their reliability and commitment to quality.
Quality Assurance Practices
To guarantee superior product outcomes, manufacturers need to implement stringent quality assurance practices. This includes regular inspections during the moulding process, as well as final product evaluations to ensure that components meet specified tolerances and durability requirements. Furthermore, adopting quality management systems (such as ISO certification) can enhance trust and reliability in the blow moulding process, ensuring manufacturers consistently deliver high-quality products.
Cost Factors in Blow Moulding Production
Several cost factors play a critical role in the overall pricing of blow moulded products. Raw material costs, labour, tooling, and mould maintenance all contribute to the final product price. Understanding these elements allows businesses to better budget for production and potentially negotiate more effectively with manufacturers. Analyzing total cost of ownership instead of solely upfront costs can lead to more informed procurement decisions and long-term savings.