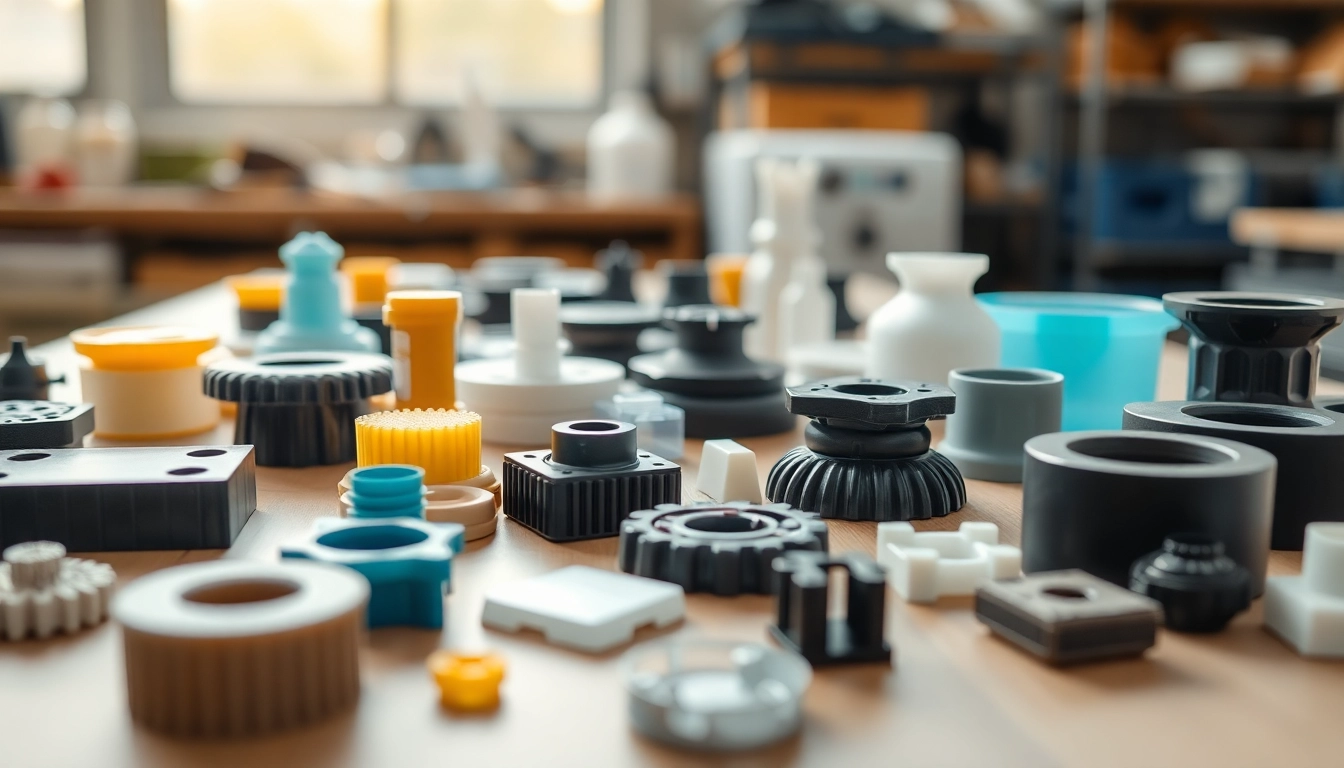
Understanding Injection Molded Parts
What Are Injection Molded Parts?
Injection molded parts are components made from a variety of materials, typically thermoplastics and thermosetting plastics, through a process known as injection molding. This manufacturing technique involves injecting molten material into a mold, where it cools and solidifies into the desired shape. Industries widely utilize injection molded parts due to their ability to produce complex geometries consistently and efficiently. The method retains precision throughout mass production, an essential factor for applications ranging from automotive to consumer goods, making injection molded parts a critical focus for engineers and designers alike.
Benefits of Using Injection Molded Parts
Injection molded parts offer numerous advantages that make them an attractive option for manufacturers:
- Cost-Effectiveness: Mass production leads to lower per-unit costs.
- Consistency and Repeatability: Injection molding delivers high precision and uniformity across large batches.
- Material Variety: A wide range of materials can be used, including various plastics and some metals.
- Complexity: The injection molding process allows for intricate designs that would be difficult to achieve with other methods.
- Quick Turnaround: Fast cycle times enable quicker production schedules and reduced lead times.
Common Materials in Injection Molding
Understanding the materials used in injection molding is vital for optimizing the performance of injection molded parts:
- Thermoplastics: The most common materials used, including ABS, polycarbonate, and polypropylene, known for their melting and solidifying properties.
- Thermosetting Plastics: Materials like epoxy or phenolic that undergo a chemical change when heated, offering better heat resistance.
- Elastomers: Flexible materials such as rubber used for components requiring elasticity.
- Bioplastics: Environmentally friendly options derived from natural materials, gaining popularity in sustainable manufacturing.
Design Considerations for Injection Molded Parts
Key Design Principles for Injection Molded Parts
Effective design for injection molded parts requires careful consideration of several principles:
- Simplicity: Designs should prioritize simplicity to reduce the complexity of the molds and minimize costs.
- Uniform Wall Thickness: Maintaining consistent thickness is essential to ensure even cooling and minimize warping.
- Incorporating Draft Angles: This allows for easier ejection of the part from the mold without damage.
- Minimizing Undercuts: Designing parts to avoid undercuts can streamline the manufacturing process.
Draft Angles and Tolerances
Draft angles—slight slopes on the sides of the mold—are crucial in facilitating the removal of the part without damaging it. Standard draft angles range from 1 to 5 degrees, depending on the complexity of the part. Understanding tolerances is equally important; tighter tolerances can increase production costs and complexity but are necessary for precision applications.
Wall Thickness and its Impact
Wall thickness directly impacts the injection molding process and the final product’s quality. Thicker walls may lead to longer cooling times and potential warping, while excessively thin walls can compromise structural integrity. Best practices suggest maintaining a thickness of 1 to 4 mm for most applications, balancing strength and processing efficiency.
The Injection Molding Process
Steps in the Injection Molding Process
The injection molding process typically follows a series of well-defined steps, as outlined below:
- Clamping: The mold halves are tightly closed using a clamping unit to withstand the high pressure during injection.
- Injection: Molten material is injected into the cavity of the mold at high speeds and pressure.
- Cooling: The molten material cools and solidifies into the shape of the mold.
- Ejection: Once cooled, ejector pins push the part out of the mold for further processing.
Cooling and Ejection of Molded Parts
The cooling phase is critical in determining the quality of injection molded parts. Efficient cooling systems, often designed into the mold, can significantly reduce cycle times and improve overall output. Following cooling, the ejection mechanism needs precision; too much force can damage the part, while too little can keep it stuck in the mold. Strategies such as using proper ejector pin placement and designing for easy release can mitigate these issues.
Quality Control Measures
Maintaining the quality of injection molded parts is paramount. Key quality control measures include:
- Regular Inspection: Frequent checks during production help identify defects early.
- Dimensional Analysis: Utilizing calipers and gauges to ensure parts meet predefined tolerances.
- Mold Maintenance: Routine cleaning and upkeep of molds prevent contamination and wear-related defects.
- Material Testing: Verifying the material properties before and after production ensures consistency and reliability.
Applications of Injection Molded Parts
Industries Utilizing Injection Molded Parts
The versatility of injection molded parts allows their use across various industries, including:
- Automotive: Components such as dashboards, bumpers, and gear knobs are commonly produced using injection molding.
- Consumer Goods: Everyday items like containers, toys, and kitchen utensils rely heavily on this manufacturing method.
- Medical Devices: Precision-engineered parts for devices like insulin pens and syringes ensure patient safety and product efficacy.
- Electronics: Housing and structural components for devices, including smartphones and laptops, utilize injection molding for efficient production.
Innovative Products Made with Injection Molding
Notable innovative products created through injection molding encompass:
- 3D Printed Molds: This advancement allows for quicker iteration and prototyping processes.
- Smart Packaging: Injection molding is utilized to create complex packaging that integrates technology for monitoring and data collection.
- Customized Robotics Parts: Advanced applications in automation leverage the unique shaping capabilities of injection molded components for robotics.
Future Trends in Injection Molded Part Applications
As industries evolve, so do the applications of injection molded parts. Future trends may include:
- Increased Sustainability: Manufacturing processes aimed at reducing environmental impact, including bioplastics and energy-efficient machinery.
- Integration of IoT: Injection molded parts will incorporate smart technologies for applications in robotics and smart home devices.
- Advanced Materials: The development of high-performance polymers that can withstand higher temperatures and pressures for specialized applications.
Choosing the Right Supplier for Injection Molded Parts
Factors to Consider When Selecting a Supplier
Selecting the right supplier for injection molded parts involves evaluating several critical factors:
- Experience and Specialization: Choose a supplier with a proven track record in your specific industry.
- Technological Capabilities: Assess the supplier’s machinery and technology to ensure they can meet your requirements.
- Quality Assurance Processes: Investigate their quality control measures to guarantee reliable outputs.
- Lead Times: Evaluate their ability to meet your timeline given your production needs.
Evaluating Supplier Capabilities
Evaluation should also consider aspects such as:
- Certifications: Look for suppliers with industry-standard certifications like ISO 9001.
- Customer Reviews: Seek testimonials or case studies that demonstrate their reliability and expertise.
- Facility Visits: If possible, visit the supplier’s facility to assess their operations firsthand.
Cost-Effectiveness in Injection Molding
Cost considerations in injection molding should encompass both initial tooling expenses and long-term part costs. It’s essential to evaluate:
- Initial Investment: The cost of molds can be substantial but is often amortized over mass production runs.
- Material Costs: Prices can vary significantly depending on the choice of materials and colorants.
- Production Volume: Higher volumes typically reduce the cost per part, making it economically feasible to invest in quality tooling.
- Post-Production Costs: Consider costs associated with finishing, assembly, and logistics when calculating total expenses.