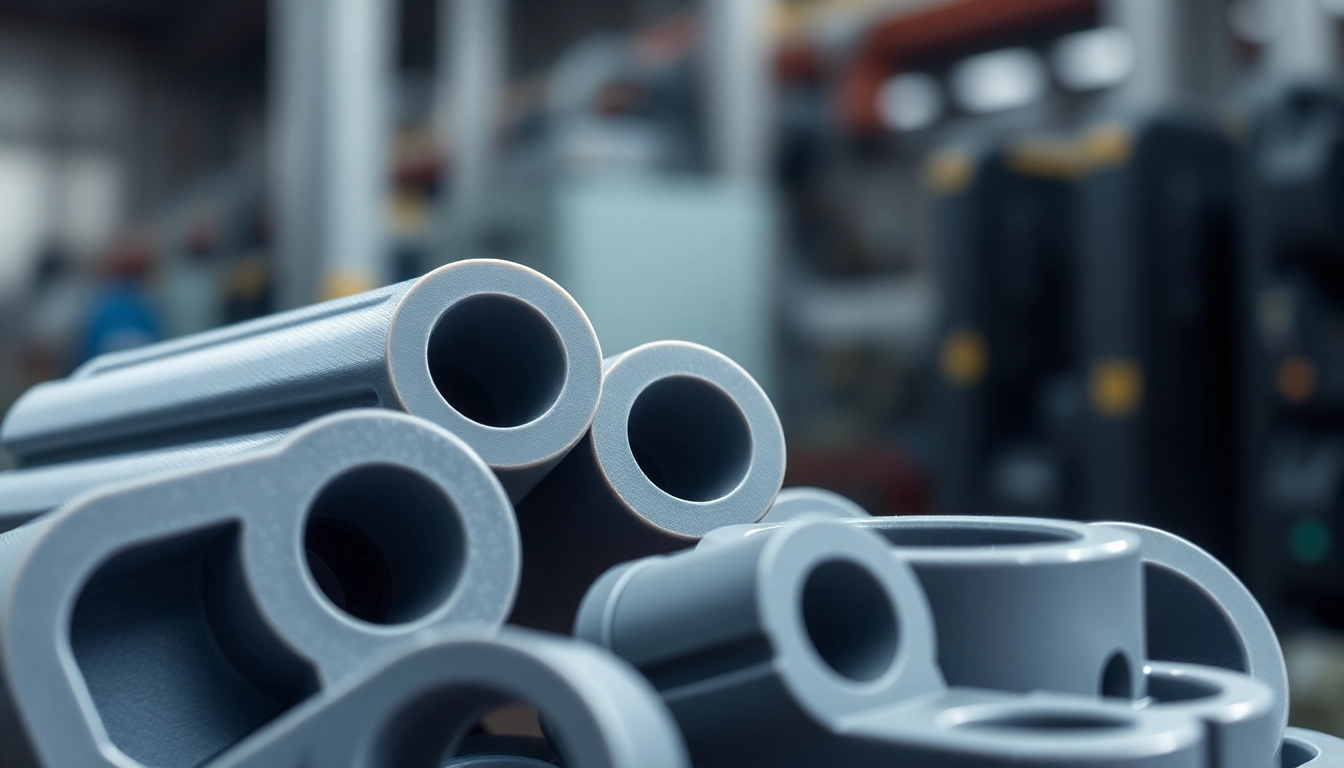
Understanding Injection Molded Parts
What are Injection Molded Parts?
Injection molded parts are components created through a highly efficient manufacturing process that involves injecting molten material, usually plastics, into a pre-designed mold. This process enables the production of complex shapes with precision, ensuring high detail and consistent quality across batches. Injection molded parts range from everyday items like plastic bottles and consumer electronics to specialized components used in industries such as automotive and healthcare. The injection molded parts play a crucial role in modern manufacturing due to their versatility and cost-effectiveness.
Significance of Injection Molding in Manufacturing
The injection molding technique has revolutionized manufacturing by allowing businesses to create large volumes of identical parts swiftly and economically. This method significantly reduces production times and labor costs compared to traditional manufacturing approaches. Furthermore, it allows for the use of advanced materials, achieving properties such as lightweight designs, strength, and resistance to chemicals. The scalability of injection molding means that products can go from concept to production efficiently without significant delays, making it indispensable for companies looking to remain competitive in today’s fast-paced market.
Key Benefits of Using Injection Molded Parts
- Cost-Effectiveness: Once the initial setup is complete, the cost per unit decreases significantly with high-volume production.
- Consistency and Quality: Precision in production ensures that each part meets strict quality control standards, minimizing the variability often seen in manual processes.
- Design Flexibility: Complex shapes and intricate designs can be easily achieved, maximizing design potential and creativity.
- Material Efficiency: The process reduces waste, making it an environmentally friendly option as compared to other manufacturing techniques.
- Speed: High production rates are achievable, enabling faster product launches and feedback cycles.
Components of Injection Molded Parts
Essential Mold Components
The successful fabrication of injection molded parts heavily relies on the intricacies of mold design. Understanding the critical components of an injection mold is necessary for achieving optimal production outcomes. Key parts include:
- Mold Base: This provides the foundation on which the entire mold system is built.
- Core and Cavity: The core creates the interior shape of the part, while the cavity defines the outer shape.
- Injection System: This part comprises the nozzle and the runner system through which the molten plastic is injected into the mold.
- Ejection System: After cooling, this system ejects the finished part, ensuring efficiency and minimal damage.
- Cooling System: Proper temperature management is essential for maintaining correct molding conditions and reducing cycle time.
Materials Used for Injection Molded Parts
The choice of material is crucial in injection molding as it impacts the performance, durability, and application of the final product. Common materials used include:
- Thermoplastics: These are the most widely used materials owing to their ease of processing and variety of properties. Examples include ABS, polypropylene, and nylon.
- Thermosetting Plastics: Once set, these materials cannot be re-melted, providing excellent hardness and thermal resistance. Common examples are epoxy and phenolic resins.
- Elastomers: These rubber-like materials offer flexibility and resilience, making them ideal for seals and gaskets.
Common Design Considerations
Designing parts for injection molding requires careful consideration to avoid costly mistakes and ensure optimal performance. Important factors include:
- Draft Angles: Incorporating 1-3 degrees of taper helps parts to be removed easily from the mold.
- Wall Thickness: Maintaining uniform wall thickness prevents warping and ensures even cooling.
- Radii and Fillets: Inside corners should be rounded to improve flow during molding and reduce stress concentrations.
- Features and Tolerances: Precise specifications should be considered to meet functional requirements without overrunning costs.
The Injection Molding Process
Step-by-Step Overview of Injection Molding
Injection molding involves a systematic process broken down into several critical stages:
- Material Feeding: Plastic pellets are fed into the hopper of the injection molding machine.
- Melting: The pellets are heated until they melt into a viscous state as they move through the barrel.
- Injection: The molten plastic is injected under high pressure into the mold cavity.
- Cooling: The injected plastic cools and solidifies within the mold.
- Ejection: The completed part is ejected, and the mold is prepared for the next cycle.
Quality Control in Injection Molded Parts Production
Quality assurance is integral to the injection molding process to uphold standards and minimize defects. Key inspection techniques include:
- Visual Inspection: Checking for surface flaws or defects immediately after ejection.
- Dimensional Measurement: Using tools such as calipers and gauges to confirm specifications.
- Mechanical Testing: Assessing properties like tensile strength and impact resistance to ensure the part meets its intended use.
Innovations in Injection Molding Technology
Recent advancements in injection molding technology have driven greater efficiency and flexibility in production. Some of these innovations include:
- 3D Printing of Molds: Rapid prototyping technologies enable faster mold production, reducing lead times significantly.
- Industry 4.0 Integration: Smart technology allows for real-time monitoring and adjustment of manufacturing processes, maximizing efficiency.
- Bio-Based Plastics: Increased usage of sustainable materials addresses environmental concerns without sacrificing performance.
Applications of Injection Molded Parts
Industry-Specific Uses
Injection molded parts find applications across a multitude of industries:
- Automotive: Components such as dashboards, bumpers, and various housings.
- Consumer Goods: Items like packaging, toys, and kitchen utensils.
- Medical Devices: Custom components for instruments and equipment, ensuring precision in healthcare applications.
- Electronics: Cases, connectors, and other housing for devices.
Case Studies of Successful Implementations
Several companies have successfully integrated injection molding to enhance their manufacturing capabilities:
For instance, a leading automotive manufacturer revamped its production line using injection molded components, which led to a reduction in weight without compromising structural integrity. This innovation not only improved fuel efficiency but also reduced costs associated with materials and assembly.
Another example includes a tech company that employed injection molding for its consumer electronics, resulting in streamlined production and enhanced product durability.
Future Trends in Injection Molding Applications
Looking ahead, several trends are likely to shape the future of injection molded parts:
- Sustainability Initiatives: A growing emphasis on eco-friendly materials and processes will dictate industry direction.
- Enhanced Automation: Increasing use of robotics and automation technology across the injection molding process for improved efficiency.
- Customization: A trend towards bespoke products with rapid prototyping will continue to rise, meeting diverse consumer demands.
Best Practices for Designing Injection Molded Parts
Common Mistakes and How to Avoid Them
Designing parts for injection molding often involves pitfalls that can lead to production inefficiencies and increased costs. Common mistakes include:
- Failure to incorporate draft angles, which can complicate part removal.
- Ignoring material flow, which could result in inconsistent part thickness.
- Overly complex designs that utilize features difficult to produce under mold constraints.
To avoid these issues, designers should engage closely with engineers to ensure feasibility from the outset, utilizing simulations and flow analysis tools.
Design Tips for Enhanced Moldability
To improve the design of injection molded parts:
- Use consistent wall thickness to enable even cooling.
- Incorporate rib designs to enhance strength without adding excessive weight.
- Consider impact resistance and stress points during design to maintain durability.
The Role of Prototyping in Design Optimization
Prototyping plays a crucial role in refining designs before mass production. It allows for testing and validation, ensuring that designs are robust and meet performance requirements. Rapid prototyping technologies like 3D printing facilitate this process, enabling companies to quickly iterate and refine designs, reducing costs and enhancing product quality.