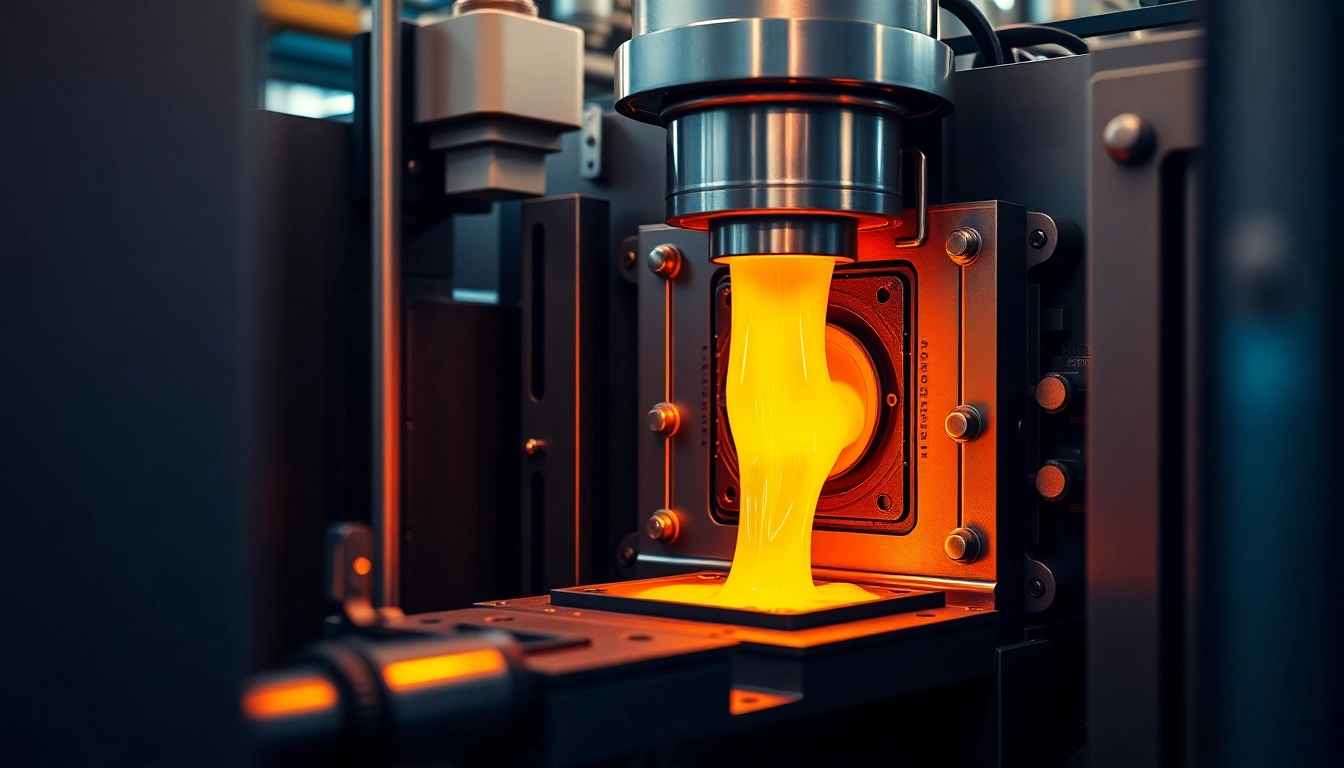
Understanding Injection Molding
Injection molding is a widely utilized manufacturing process that produces parts by injecting molten materials into a mold. This technique is favored across numerous industries, from automotive to consumer goods, due to its efficiency and ability to create complex geometries with precision. Recognizing the significance of injection molding, this comprehensive guide takes an in-depth look at the process, its advantages, common applications, and emerging trends. If you’re looking to enhance your knowledge on injection molding, you’ve come to the right place.
What is Injection Molding?
At its core, injection molding is a manufacturing process that involves converting raw materials, typically thermoplastics, into solid products. The process begins by heating the material until it melts, after which it is forced into a mold under high pressure. The material then cools and solidifies, taking the shape of the mold. This method allows for the mass production of intricate parts with high levels of consistency and repeatability.
The History and Evolution of Injection Molding
The origins of injection molding can be traced back to the 19th century when the first patented injection molding machine was created in 1872 by John Wesley Hyatt. Initially designed to inject celluloid into a mold for creating billiard balls, the process evolved over the years to accommodate various thermoplastics and metals. By the mid-20th century, advancements in polymer chemistry and machine technology led to the ability to produce large numbers of parts with improved quality and efficiency. Today’s injection molding processes incorporate sophisticated technologies, including computer-aided design (CAD) and automation, further enhancing precision and reducing production time.
Common Applications of Injection Molding
Injection molding is utilized in a vast array of industries due to its versatility. Some common applications include:
- Automotive Components: Manufacturing dashboards, panels, and various internal components that require durability and aesthetic appeal.
- Consumer Goods: Producing everyday items such as containers, toys, and kitchenware that require intricate designs and colors.
- Medical Devices: Creating medical equipment, such as syringes and surgical tools, where precision and hygiene are critical.
- Electronics: Molding casings and components for devices like smartphones and computers, which demand high-quality finishes.
The Injection Molding Process Explained
Stages of the Injection Molding Process
The injection molding process can be broken down into several key stages:
- Clamping: The mold is securely closed before the injection begins. The clamping force must be sufficient to withstand the pressure exerted during injection.
- Injection: The molten material is injected into the mold at high speed and pressure, filling the cavity to achieve the desired shape.
- Cooling: The mold is cooled to solidify the plastic. This stage is crucial for achieving dimensional accuracy and part integrity.
- Ejection: Once cooled, the mold opens, and the finished product is ejected. Ejector pins or plates are typically used to facilitate this process.
Materials Used in Injection Molding
A wide variety of materials can be employed in the injection molding process. These primarily include:
- Thermoplastics: Commonly used materials such as ABS (acrylonitrile butadiene styrene), polycarbonate, and polypropylene.
- Thermosets: Materials that harden when heated and are utilized for high-temperature applications, like polyurethanes.
- Elastomers: Flexible materials used to produce soft parts such as seals and gaskets.
- Bio-based plastics: Increasingly popular due to sustainability efforts, these materials are derived from renewable resources.
Quality Control in Injection Molding
Ensuring the quality of injection molded parts is crucial for maintaining the standards expected by industries. Quality control processes typically involve:
- Visual Inspection: Checking parts for visible defects such as surface irregularities or color mismatches.
- Dimensional Checks: Utilizing tools such as calipers and gauges to confirm that parts meet specified dimensions.
- Functional Testing: Performing tests under operational conditions to verify that parts function as intended.
- Material Testing: Analyzing the physical properties of the material to ensure they meet industry standards and specifications.
Advantages of Injection Molding over Other Methods
Cost-Effectiveness in Mass Production
One of the most significant advantages of injection molding is its cost-effectiveness, particularly in mass production runs. The ability to produce large quantities of identical parts reduces the cost per unit, making it an attractive option for businesses. While initial setup costs are higher due to mold creation, the long-term savings achieved through reduced material waste and increased efficiency drive down production costs.
Complexity and Design Flexibility
Injection molding allows for an extensive range of designs and geometries, accommodating intricate features such as undercuts and varying wall thicknesses. This flexibility enables designers to create innovative product designs that would be challenging or impossible using other methods, thereby enhancing product functionality and aesthetics.
Lower Waste and Material Efficiency
Compared to alternative manufacturing methods, injection molding generates significantly less waste. The process enables precise control over material usage, and any excess can often be recycled and reused, contributing to sustainability efforts. This efficiency not only reduces overall production costs but also minimizes environmental impact.
Challenges and Solutions in Injection Molding
Common Defects in Injection Molding
Despite its advantages, injection molding is not without challenges. Some common defects that may occur include:
- Warpage: A distortion of the molded part caused by uneven cooling or internal stresses.
- Sink Marks: Dents on the surface of a part resulting from material shrinking during the cooling process.
- Flash: Excess material that escapes the mold, leading to unwanted projections on the part.
- Bubbles or Voids: Air trapped within the part during injection, which can affect performance and appearance.
Strategies for Minimizing Defects
To address these challenges, manufacturers can implement several strategies:
- Optimizing Cooling Times: Adjusting mold temperature and cooling times can help reduce warpage and enhance part quality.
- Precision Mold Design: Investing in high-quality molds with precise tolerances can minimize defects such as flash and sink marks.
- Material Selection: Choosing appropriate materials with suitable flow characteristics can aid in achieving optimal part quality.
- Regular Maintenance: Performing regular maintenance on injection molding machines and molds ensures consistent performance and reduces downtime.
Future Innovations in Injection Molding Technology
As industries continue to evolve, injection molding technology is also advancing. Innovations such as:
- 3D Printing: Integration of 3D printing technology into the injection molding process allows for quicker mold prototyping and design iterations.
- Smart Manufacturing: The use of IoT and AI technologies can enhance predictive maintenance, quality control, and overall efficiency through data analysis.
- Sustainability Initiatives: Development of biodegradable and recyclable materials is gaining traction, promoting environmentally friendly practices in injection molding.
Conclusion: The Future of Injection Molding in Manufacturing
Emerging Trends in Injection Molding
The injection molding industry is witnessing a transformation shaped by technology and sustainability. As companies seek efficient production methods that minimize waste and environmental impact, advancements in materials and processes will continue to drive growth. Additionally, the trend towards customization is prompting manufacturers to adopt more flexible production techniques.
Investment in Technology and Training
For businesses to remain competitive in an evolving industry, investing in advanced machinery, training for employees, and up-to-date technologies is essential. Manufacturers must ensure their workforce is adept at leveraging new tools and techniques, allowing them to harness the full potential of modern injection molding practices.
The Role of Sustainability in Injection Molding
As sustainability takes precedence in global markets, the injection molding industry is responding by adopting greener practices. From the development of bio-based materials to the implementation of efficient production processes, the commitment to minimizing environmental impact is at the forefront of the industry’s future. Embracing sustainability not only meets regulatory requirements but also resonates with the increasing demands of environmentally conscious consumers.