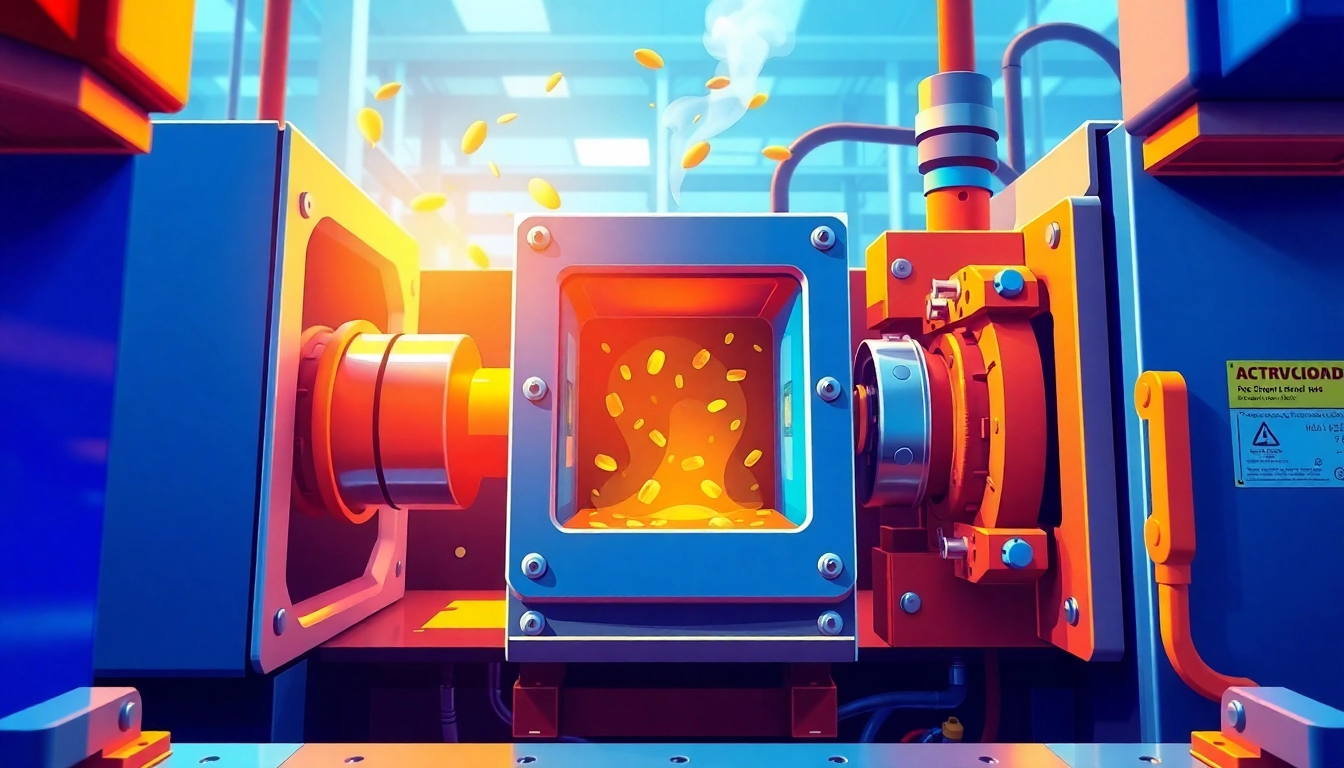
Understanding Injection Molding
Injection molding is a critical manufacturing process that allows industries to produce parts efficiently and at scale. This technique has transformed the way plastic products are created, enabling the production of intricately designed items with consistency and accuracy. In this comprehensive guide, we will delve into the various aspects of injection molding, exploring its process, advantages, challenges, and its place in modern manufacturing.
What is Injection Molding?
Injection molding is a manufacturing process where molten material, usually plastic, is injected into a mold to create specified shapes. The process begins with the heating of plastic granules until they become malleable, followed by injection into a mold. Once cooled, the material solidifies to form the desired part. This method is exceptionally popular for mass production, allowing for high efficiency and uniformity across multiple products. Used widely in industries such as automotive, medical, and consumer goods, injection molding is renowned for its ability to produce complex geometries that would be difficult to achieve with other manufacturing processes.
Key Components of the Process
The injection molding process comprises several integral components, each playing a vital role in the entire workflow:
- Injection Molding Machine: The core of the process, consisting of an injection unit and a clamping unit. The injection unit melts the plastic, while the clamping unit holds the mold in place during production.
- Molds: Custom-designed metal molds that provide the shape of the final product. Molds are typically made from steel or aluminum and can be quite expensive to produce.
- Raw Materials: Generally, thermoplastics are used for injection molding. The choice of plastic affects the part’s properties, cost, and production speed.
- Cooling Systems: Vital for regulating the temperature of the mold, ensuring that the plastic solidifies correctly and avoids defects.
Applications Across Industries
Injection molding serves a multitude of industries. Its versatility extends from manufacturing tiny components for electronics to creating large automotive parts. Here are some notable applications:
- Automotive: Parts such as dashboards, bumpers, and interior fittings are manufactured using injection molding for efficiency and weight reduction.
- Medical: Sterile equipment, including syringes and surgical instruments, are produced with precision for essential health applications.
- Consumer Products: Everyday items, from toys to kitchenware, take advantage of injection molding for cost-effective mass production.
- Electronics: Housing and casings for electronic devices benefit from the high tolerance and intricate designs achievable through this process.
The Injection Molding Process Explained
Stages of Injection Molding
The injection molding process unfolds in a series of carefully controlled stages:
- Clamping: The mold is securely closed by the clamping unit, ensuring it remains shut during the injection of molten plastic.
- Injection: Molten plastic is injected into the mold cavity through a nozzle, filling it under high pressure.
- Cooling: The injected plastic is cooled, causing it to solidify and take the shape of the mold.
- Ejection: Once cooled, the mold opens, and ejector pins release the newly formed part.
Choosing the Right Materials
The choice of material in injection molding significantly impacts the final product’s performance, cost, and appearance. Common materials include:
- Thermoplastics: These materials can be melted and molded repeatedly. Examples include polyethylene (PE), polypropylene (PP), and polystyrene (PS).
- Thermosetting Plastics: Once set, these materials cannot be remelted. They are used for items that require durability, such as electrical sockets.
- Elastomers: These are flexible materials ideal for applications needing rubber-like properties, such as seals and gaskets.
Common Challenges and Solutions
While injection molding is efficient, it is not without its challenges. Some common issues include:
- Injection Molding Defects: Problems like warping, flash, and short shots can occur. Regular maintenance of the machine and proper mold design can mitigate these issues.
- Material Shortages: Global supply chain disruptions can lead to difficulty in sourcing materials. Building strong supplier relationships can help navigate these challenges.
- High Initial Costs: The cost of producing molds can be quite high. However, the long-term production efficiency often offsets these initial expenses.
Advantages of Injection Molding
Cost-Effectiveness in Production
One of the significant benefits of injection molding is its cost-effectiveness for large-scale production. The initial investment in molds is high, but the cost per unit decreases significantly as production volumes increase. This economy of scale makes it an attractive choice for manufacturers looking to produce large quantities of uniform parts.
Producing Complex Shapes
Injection molding is unparalleled in its ability to create intricate shapes and designs. The process can produce parts with complex geometries that are challenging to achieve through other manufacturing techniques like machining or extrusion. This capability opens up more possibilities for product designers and engineers.
High Volume Yield
With capabilities to produce thousands to millions of parts consistently, injection molding is one of the most efficient production techniques available. The rapid cycle times ensure that businesses can meet high market demands without compromising quality.
Best Practices for Successful Injection Molding
Design Considerations for Molds
The design of the molds is crucial for successful injection molding. Designers should consider:
- Parting Lines: Proper placement of parting lines is essential to ensure easy ejection of the finished parts.
- Draft Angles: Incorporating draft angles facilitates the mold release and prevents damage during the ejection process.
- Uniform Wall Thickness: Designing parts with consistent wall thickness reduces internal stresses and minimizes defects.
Quality Control Measures
Implementing stringent quality control measures ensures that the produced parts meet the required specifications. This can involve:
- Regular Inspections: Regular measurement and inspection of parts during production help detect issues early on.
- Statistical Process Control (SPC): Analyzing production data to identify trends or abnormalities that may indicate a problem.
Maintaining Equipment Efficiency
Regular maintenance of the injection molding equipment is vital for longevity and efficiency. This includes:
- Scheduled Maintenance: Setting up a schedule for routine checks and maintenance can prevent unexpected downtime.
- Operator Training: Ensuring operators are well-trained in both the operation and basic maintenance of the machinery can enhance efficiency and safety.
The Future of Injection Molding
Innovations in Technology
The injection molding industry is continuously evolving, embracing new technologies such as:
- Industry 4.0: Smart manufacturing technologies, like IoT (Internet of Things), allow for real-time monitoring and automation, enhancing efficiency.
- 3D Printing: Integrating 3D printing with traditional injection molding opens possibilities for rapid prototyping and customized mold creation.
Sustainability and Eco-Friendly Practices
As industries become increasingly focused on sustainability, so too is injection molding evolving. Practices such as using recycled materials and reducing waste during production are becoming standard. Manufacturers are exploring bioplastics as alternatives to traditional plastics, creating biodegradable options that align with growing environmental concerns.
Emerging Markets and Trends
Global demand for injection-molded products continues to rise, driven by growing markets in Asia and Africa where manufacturing capabilities are expanding. Innovations in design, materials, and production methods will shape the future of injection molding, leading to more efficient and effective manufacturing processes.