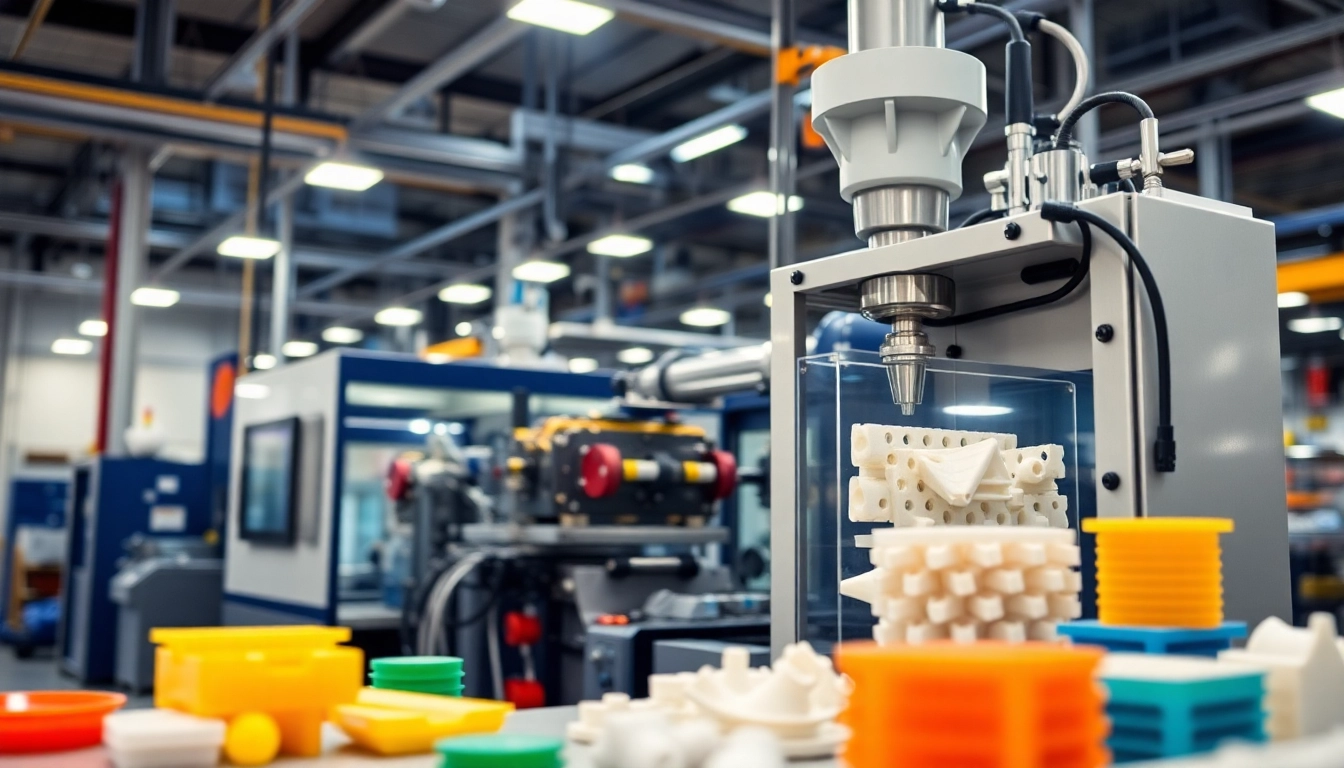
Understanding the Basics of Plastic Part Manufacturing
The manufacturing of plastic parts is a critical process that serves various industries, from automotive to electronics, healthcare to packaging. It involves several manufacturing techniques that can be tailored to meet the specific requirements of different applications. For anyone looking to understand the complexities involved in the manufacture of plastic parts, it’s essential to have a grasp of the various methods, materials, and challenges that define this industry.
Overview of Plastic Manufacturing Processes
Plastic manufacturing encompasses various processes, including but not limited to:
- Injection Molding: This is the most common method where molten plastic is injected into a mold to create specific shapes.
- Extrusion: In this method, plastic material is melted and formed into continuous shapes by forcing it through a die.
- Blow Molding: Suitable for creating hollow plastic products like bottles, this method involves inflating hot plastic inside a mold.
- Thermoforming: This involves heating a plastic sheet until pliable, followed by forming it into various shapes using molds.
- Vacuum Forming: Similar to thermoforming, vacuum forming uses air pressure to pull the heated plastic into the mold.
- Compression Molding: In this technique, plastic is placed in an open mold and then heated until it becomes pliable.
Key Materials Used in Production
The selection of materials is crucial in the manufacture of plastic components. Some of the most common materials include:
- Thermoplastics: These can be melted and reshaped multiple times. Examples include polyethylenes (PE), polypropylenes (PP), and polyvinyl chloride (PVC).
- Thermosetting Plastics: These materials undergo a chemical change when heated and cannot be remolded. Common examples include epoxy and phenolic resins.
- Elastomers: Known for their elastic properties, elastomers are increasingly being used in applications requiring stretch and flexibility, such as seals and gaskets.
Common Challenges in the Manufacture of Plastic Parts
Plastic part manufacturing can be fraught with challenges. Some of the most common issues faced by manufacturers include:
- Material Shortage: Fluctuations in the availability of raw materials can disrupt production.
- Quality Control: Ensuring consistency in quality across batches is pivotal.
- Cost Management: Balancing production costs while maintaining quality standards can be difficult.
- Environmental Regulations: Compliance with environmental laws requires ongoing attention and adaptation.
Injection Molding: A Deep Dive
Process Overview and Benefits
Injection molding is a favored method for producing a vast variety of plastic parts. The primary advantage of this process is its efficiency and ability to produce complex geometries at a high volume. The basic steps in injection molding include:
- Material Preparation: The chosen plastic resin is fed into a hopper and then melted in a heated barrel.
- Injection Phase: The molten plastic is injected under high pressure into a precisely machined mold.
- Cooling Phase: Once the material has cooled sufficiently to solidify, the mold is opened to eject the part.
One of the key benefits of injection molding is the ability to produce large quantities of parts with minimal repeatability issues, translating into lower per-unit costs.
Optimal Design Considerations for Molding
Design plays a significant role in the success of injection molded parts. Here are optimal design tips:
- Uniform Wall Thickness: Maintaining a consistent wall thickness minimizes stress and warpage during cooling.
- Draft Angles: Incorporating draft angles facilitates easier ejection from the mold.
- Rounding Edges: Rounded edges can help prevent stress concentrations, which may lead to cracking or breaking.
Case Studies of Successful Injection Molded Parts
Examining successful applications of injection molded parts can provide valuable insights into the method’s versatility:
- Automotive Components: Many automotive parts such as bumpers, dashboards, and housings are mass-produced using injection molding due to their durability and aesthetic consistency.
- Consumer Products: Items like kitchenware, toys, and electronic casings benefit from the high precision that injection molding offers.
Alternative Manufacturing Techniques for Plastic Parts
Plastic Extrusion and Its Applications
Plastic extrusion is suitable for creating long, continuous shapes. Its applications often include:
- Railings and Fencing
- Packaging Films
- Pipe and Tubing
The process allows for high production rates and can incorporate various kinds of materials, including recycled plastics.
Other Techniques: Blow Molding and 3D Printing
Two other remarkable techniques noteworthy for their applications and benefits are:
- Blow Molding: Particularly effective for hollow shapes, this method is extensively used in packaging bottles. The recycling process also allows manufacturers to produce eco-friendly products from recycled materials.
- 3D Printing: A rapidly growing method allowing for rapid prototyping and complex geometrical designs that were once impossible with traditional methods.
Choosing the Right Method for Your Project
Selecting the appropriate manufacturing technique is crucial for project success. Considerations should include:
- Production Volume
- Complexity and Size of Parts
- Material Availability and Costs
A well-informed decision can yield optimal performance, quality, and cost-effectiveness.
Quality Control in Plastic Manufacturing
Defining Quality Standards for Plastic Parts
Establishing quality standards is vital for the consistency and reliability of the manufactured plastic parts. Common standards include:
- ISO 9001 for Quality Management Systems
- ASTM Standards for Material Specifications
- RoHS Compliance for Toxic Substances
Testing Methods and Best Practices
Different testing methods are essential to ensure product quality, including:
- Dimensional Verification: Ensures that the parts meet specified dimensions and tolerances.
- Material Testing: Conduct tests such as tensile strength and impact resistance.
- Visual Inspection: Manual checks for surface finishes, color consistency, and defects.
Continuous Improvement Strategies
Adopting a culture focused on continuous improvement can elevate quality and efficiency. Techniques include:
- Lean Manufacturing: Eliminating waste and optimizing production processes.
- Six Sigma: Using data-driven methods to improve quality by identifying and removing causes of defects.
The Future of Plastic Part Manufacturing
Emerging Technologies and Innovations
The future of plastic manufacturing is bright, with technology paving the way for new possibilities. Innovations like automation in factories, enhanced precision molding, and the potential for using bio-based plastics are at the forefront of this evolution.
Sustainability in the Plastic Industry
With growing concerns about environmental impact, sustainability is increasingly critical. Strategies include:
- Utilizing recycled materials in production
- Developing biodegradable plastics
- Implementing sustainable sourcing and production practices
Market Trends and Predictions
Looking ahead, the plastic parts manufacturing landscape is expected to witness significant changes due to:
- Increased demand for lightweight materials in automotive and aerospace sectors
- Advancements in customization and personalization through 3D printing technologies
- Rising legislative pressures for reduced waste and increased recycling practices
Staying ahead of these trends will be essential for manufacturers who wish to remain competitive in this dynamic industry.