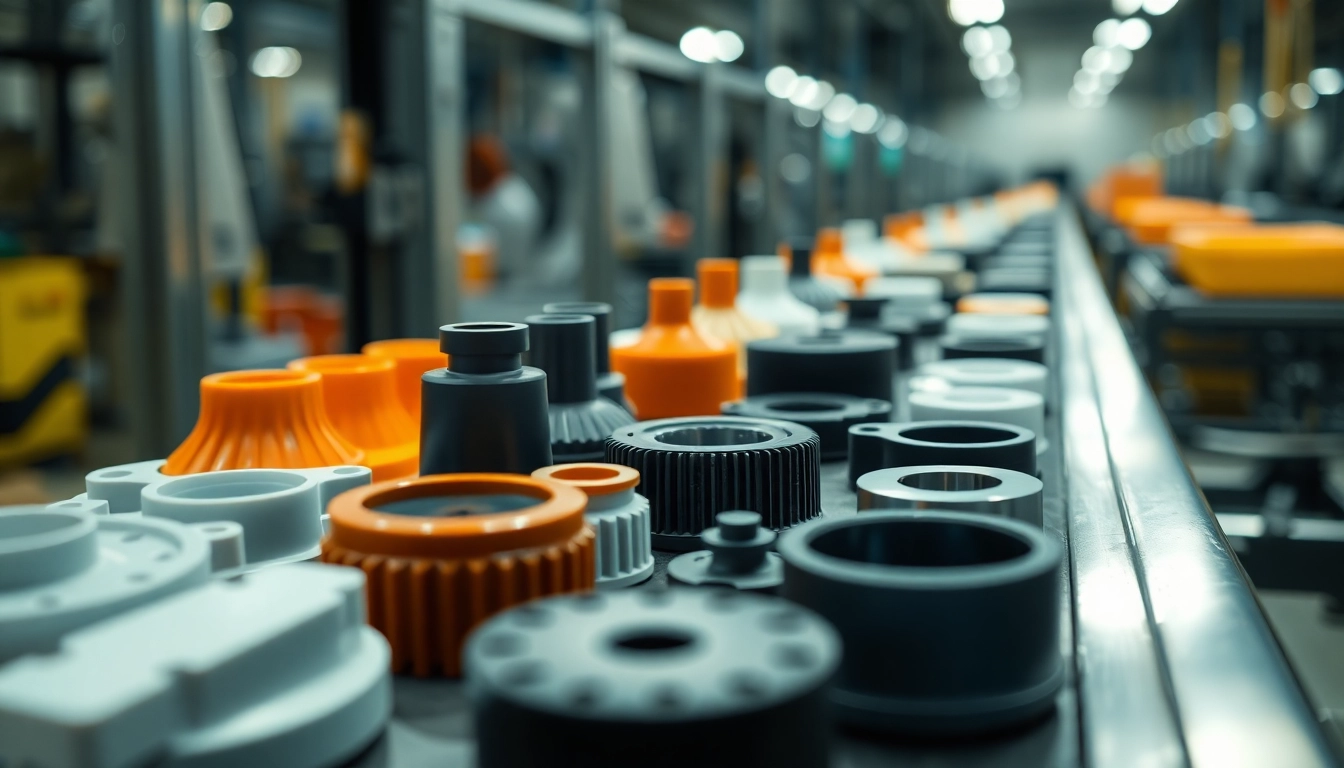
Understanding Injection Molded Parts
What Are Injection Molded Parts?
Injection molded parts are products manufactured using a process that involves injecting molten material—commonly plastic—into a pre-designed mold. This method is integral to modern manufacturing across various industries, including automotive, consumer electronics, and medical devices. One of the distinct advantages of injection molding is its ability to produce complex shapes with high precision and reproducibility. An array of products, from tiny components in electronic devices to large automotive parts, can be manufactured through this innovative technology. For a deeper dive into how these parts are made, check out this resource on injection molded parts.
The Injection Molding Process Explained
The injection molding process consists of several stages:
- Material Preparation: The process begins with the selection and preparation of raw materials—usually granules of thermoplastic or thermosetting resins. These materials are heated until they melt, making them malleable for injection.
- Injection Phase: The molten material is then injected into the mold cavity under high pressure. The force of injection ensures that the material fills every part of the mold, including intricate designs and details.
- Curing or Cooling: Once the mold is filled, the material is allowed to cool. This solidification process ensures that the product retains the mold shape. The cooling time can vary based on part dimensions and material properties.
- Mold Opening: After cooling, the mold is opened to release the newly formed part. This is typically done using ejector pins that push the product out of the mold cavity.
- Finishing Operations: The final stage may involve trimming, surface finishing, or adding colors. Some complex parts might also undergo secondary processes, such as assembly or machining, to meet specific demands.
Advantages of Using Injection Molded Parts
Injection molding offers numerous advantages, making it a preferred manufacturing method in many sectors:
- High Efficiency: Once set up, injection molding is capable of producing large volumes of parts rapidly, resulting in low per-piece costs.
- Complex Geometries: The process can easily produce intricate shapes and designs that may be difficult, time-consuming, or costly to create through other manufacturing methods.
- Material Variety: A wide range of materials can be used for injection molding, including various plastics, elastomers, and even metals for specific applications.
- Consistency and Quality: The automated nature of the process leads to high consistency in part dimensions and surface finish, ensuring quality across all produced items.
- Minimal Waste: Injection molding generates minimal waste material since most of the unused material can be recycled and reused in future processes.
Key Components in Injection Molding
Parts of an Injection Mold and Their Functions
Understanding the components of an injection mold is pivotal to grasping how the manufacturing process works. Key parts include:
- Mold Base: This is the frame upon which the mold components are mounted. It provides stability and alignment during the injection process.
- Cavity and Core: The cavity is the part of the mold that creates the exterior surface of the component, while the core forms the internal details.
- Ejector Pins: These components assist in removing the molded parts from the mold once they have cooled and solidified.
- Sprue and Runner Systems: The sprue is the channel through which molten material flows into the mold. The runner system distributes the material evenly to different parts of the mold.
- Cooling Channels: Integrated within the mold, cooling channels help regulate temperature, ensuring a consistent and efficient cooling process.
Choosing the Right Materials for Your Molded Parts
Selecting the appropriate material for injection molded parts is crucial and depends on various factors, including:
- Mechanical Properties: Consider the strength, flexibility, and durability required for the final product. Materials like ABS, polycarbonate, and nylon are popular choices due to their favorable mechanical properties.
- Thermal Resistance: Depending on the application, the material may need to withstand high temperatures. Choices such as high-temperature polyamides can offer excellent thermal stability.
- Cost Considerations: Material costs can vary significantly, so budget constraints often play a role in material selection.
- Color and Finish: Some materials can be pigmented, allowing for specific color requirements. Surface finish options should also be considered based on aesthetic and functional needs.
Common Issues and Solutions in Injection Molding
Despite its advantages, injection molding is not without challenges. Here are some common issues, their causes, and potential solutions:
- Warpage: This occurs when a part is distorted after being removed from the mold. Solutions include optimizing the cooling process, adjusting the mold design, or selecting materials with better dimensional stability.
- Flash: Occurs when molten material spills out of the mold. This can be mitigated by improving mold alignment and clamping force.
- Bubbles and Voids: These defects can result from trapped air in the mold. Solutions involve improving venting in the molds or adjusting injection speeds.
- Surface Defects: Issues like scratches or blemishes on the part surface can arise from improper handling or mold wear. Routine maintenance and refining handling procedures can help prevent these problems.
Applications of Injection Molded Parts
Industries That Use Injection Molded Components
Injection molded parts find applications in numerous industries due to their versatility:
- Automotive: Injection molding is extensively used to produce components such as bumpers, dashboards, and interior fittings that require precision and durability.
- Consumer Electronics: Many electronic devices incorporate injection molded parts for housings, connectors, and inner components.
- Healthcare: Medical devices often utilize injection molding due to its ability to deliver high-quality parts that comply with stringent regulatory requirements.
- Household Goods: Everyday items like containers, kitchen utensils, and toys are commonly made using this technology, benefitting from the cost efficiency and production speed offered by injection molding.
Everyday Products Made from Injection Molding
Some common household items produced through injection molding include:
- Plastic bottles and caps
- Food storage containers
- Household appliances like blenders and microwaves
- Automobile components such as plastic fittings and interior components
Custom Solutions for Special Applications
The flexibility of injection molding also allows for the development of custom solutions tailored to specific needs. Companies often work with injection molding specialists to design unique molds that meet particular operational or aesthetic requirements. This might include:
- Specialized Shapes: Creating complex geometries that can’t be achieved through traditional manufacturing.
- Multi-Material Injection Molding: Combining different materials or colors in a single part to enhance functionality or appeal.
- Rapid Prototyping: Using injection molding technology to create prototypes quickly for testing or design validation before moving to full-scale production.
Design Considerations for Injection Molded Parts
Best Practices for Designing Molded Parts
Designing parts for injection molding comes with its own set of strategies. Some best practices include:
- Draft Angles: Incorporate draft angles in the design to facilitate easier removal from the mold.
- Uniform Wall Thickness: Ensure that wall thickness remains consistent to avoid issues like warping or uneven cooling.
- Incorporate Ribs: Adding ribs can enhance the strength of the part without significantly increasing the material used.
How to Optimize Your Design for Manufacturing
Optimization is crucial to ensuring that designs are not only aesthetically pleasing but also manufacturable. Considerations include:
- Material Flow: Analyze how the molten material will flow through the mold to ensure complete filling.
- Mold Cost: Evaluate the complexity of the mold design to balance production costs with functional requirements.
- Functional Testing: Prior to finalizing designs, prototypes should be tested to evaluate functionality and fit.
Importance of Tolerances and Specifications
A clear set of tolerances and specifications is vital in any injection molding project. Specified tolerances ensure that parts fit correctly into their intended applications. Key focus areas include:
- Dimensional Tolerances: Define allowable variations in dimensions to ensure that every part meets the assembly requirements.
- Surface Finish Requirements: Outlining the acceptable finish will impact the aesthetics and functionality of the final product.
- Material Properties: Specify the necessary characteristics of the raw materials in terms of strength, heat resistance, and durability based on end-use.
Future Trends in Injection Molding Techniques
Advancements in Materials for Injection Molded Parts
The landscape of materials used in injection molding is continually evolving. Recent advancements include:
- Biodegradable Plastics: As sustainability becomes a priority, there is a growing trend towards using biodegradable materials in injection molding, reducing environmental impact.
- High-Performance Polymers: Innovations in high-performance polymer materials that can withstand extreme conditions are on the rise, allowing for new application areas.
- Smart Materials: The development of smart materials may allow for functionality that changes in response to environmental stimuli, opening doors for new product designs.
Smart Manufacturing Technologies in Injection Molding
Emerging technologies are revolutionizing injection molding, including:
- Automation: Robotics and automation systems are increasing efficiency, reducing production times, and improving worker safety.
- Data Analytics: Utilizing big data to optimize the injection molding process has improved production efficiency and reduced waste.
- Internet of Things (IoT): IoT technologies enable real-time monitoring and control of the injection molding process, ensuring enhanced quality and reduced downtime.
Sustainability Practices in the Injection Molding Industry
Sustainability is swiftly becoming a core focus within the injection molding sector. Practices include:
- Recycling and Reusing Materials: More manufacturers are adopting circular economy practices, ensuring that leftover materials are recycled or reused.
- Energy Efficiency: Innovative machines designed for energy efficiency are minimizing the carbon footprint of production processes.
- Green Manufacturing Initiatives: Companies are increasingly integrating environmentally friendly practices into their production methods, from sourcing sustainable materials to minimizing waste.