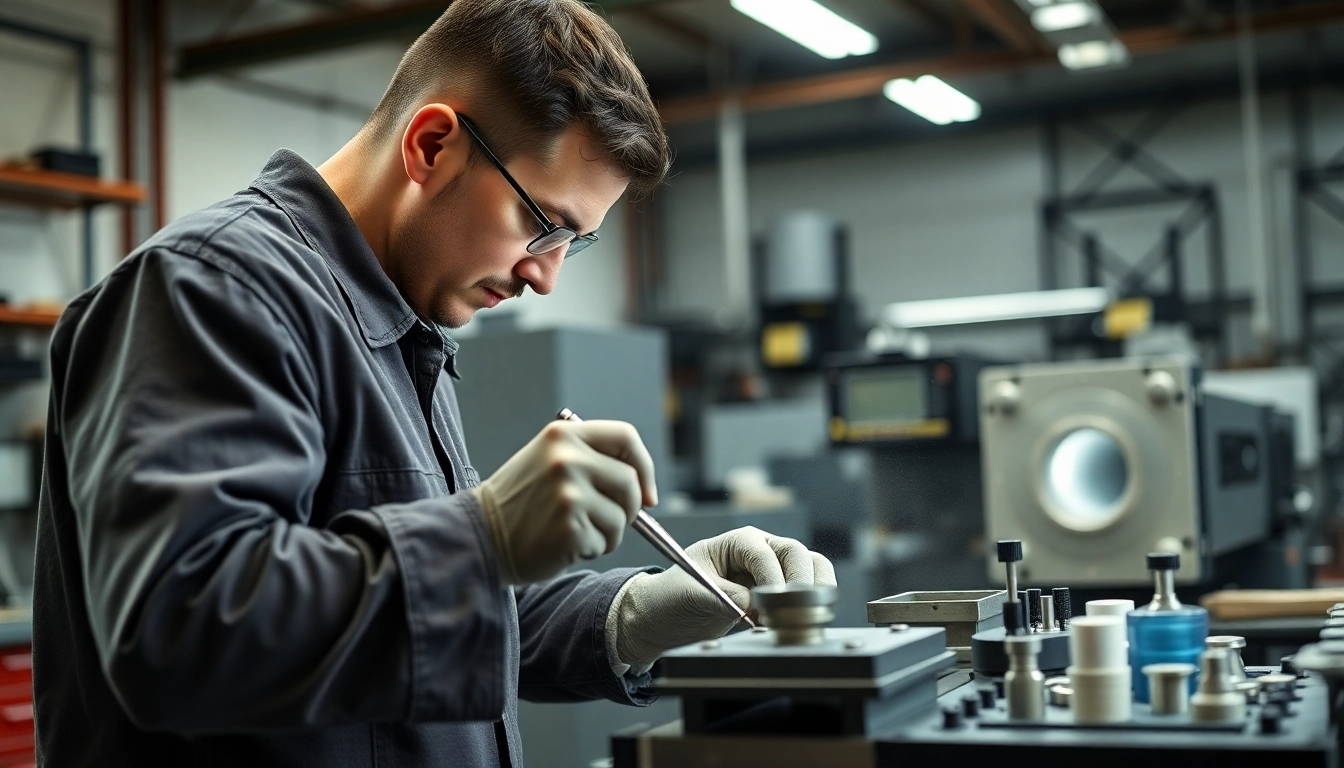
Understanding the Role of a Mold Maker for Injection Molding
The world of manufacturing is complex, with a variety of processes that transform raw materials into final products. At the heart of many of these processes is the mold maker for injection molding, a skilled professional whose expertise is crucial in creating the molds used to produce intricate plastic components. This article aims to delve into the significance of mold makers, the processes they utilize, and how selecting the right professional can elevate product quality and efficiency. For a deeper dive into mold making techniques and strategies, you can explore mold maker for injection molding.
What Does a Mold Maker Do?
A mold maker specializes in designing, fabricating, and maintaining molds used in injection molding processes. This profession demands a blend of artistic and technical skills, involving the creation of precise molds that can produce intricate parts repeatedly and efficiently. The role varies widely based on project requirements but generally includes:
- Designing Molds: Mold makers collaborate with engineers and product designers to establish the specifications and design blueprints for molds.
- Fabricating Molds: The actual fabrication involves using various materials and techniques, including metal machining and additive manufacturing, to create the mold components.
- Testing and Refinement: Once a mold is fabricated, the mold maker conducts tests to ensure functionality and quality, making adjustments as necessary.
- Maintenance: Regular upkeep and repair of molds are essential to prolong their lifespan and ensure consistent product quality.
Key Skills Required for Mold Making
To excel as a mold maker, specific skills and knowledge are essential:
- Technical Proficiency: A strong understanding of materials, design principles, and engineering concepts is crucial.
- CNC and Machining Skills: Familiarity with computer numerical control (CNC) machines and traditional machining is vital, as these tools are central to mold fabrication.
- Attention to Detail: Precision is paramount in mold making. The ability to focus on minute details can significantly impact the quality of the final product.
- Problem-Solving Skills: Building molds often involves overcoming unexpected challenges and finding innovative solutions efficiently.
The Importance of Precision in Injection Molding
Precision in mold making isn’t merely about meeting specifications; it’s about ensuring the end product is fabricated accurately and consistently. Molds must fit together perfectly to avoid defects in molded parts, which could lead to costly production delays or product failures. Achieving this level of precision requires a combination of skill, advanced machinery, and thorough quality control measures.
Types of Injection Molding Processes
Understanding the various injection molding processes is essential for mold makers, as each type presents different challenges and requires specific mold designs.
Standard Injection Molding
Standard injection molding is the most common method. In this process, molten plastic is injected into a mold and allowed to cool, forming the desired shape. Mold makers must consider factors like cooling time, material shrinkage, and mold release properties when designing for this process.
Injection Blow Molding Explained
Injected blow molding combines the principles of injection molding and blow molding to create hollow plastic products. It involves injecting molten plastic into a mold, where it is then inflated to form its final shape. Mold makers need to design molds that can accommodate the necessary air channels and create uniform wall thicknesses.
Considerations for Multi-Cavity Molds
Multi-cavity molds are crucial for mass production as they enable the simultaneous creation of multiple parts in a single cycle. However, designing these molds can be complex. Mold makers must ensure that each cavity achieves the same quality and finish, managing flow rates and cooling to achieve uniformity across all parts.
Choosing the Right Mold Maker for Your Needs
When selecting a mold maker, it’s not just about finding a skilled professional; it’s about choosing the right fit for your specific project needs. Here are critical considerations:
Experience and Expertise in Mold Making
The mold maker’s experience should align with your project scale and complexity. Look for professionals who have worked on similar projects or industries. Inquire about their previous work, understanding how their experience can add value to your specific needs.
Evaluating Reviews and Case Studies
Reviews and case studies provide insight into a mold maker’s capabilities. Look for customer feedback that highlights their reliability, quality of work, and problem-solving abilities. Request case studies that showcase their approach to challenges similar to those your project might face.
Comparing Costs and Value Propositions
Cost is a significant factor when selecting a mold maker, but it shouldn’t be the only consideration. A lower-cost option might compromise quality or lead to higher maintenance costs down the road. Compare the value propositions of different mold makers to discern which offers the best balance of cost, quality, and service.
Best Practices for Working with a Mold Maker
Collaboration with a mold maker involves clear communication and efficient project management to ensure optimal results. Consider the following best practices:
Effective Communication and Project Management
Open lines of communication are critical throughout the mold making process. Regular updates and discussions help ensure that the project stays on track and meets your expectations, allowing for adjustments when necessary.
Preparing Detailed Specifications
Accurate and comprehensive specifications document every aspect of the project—from material requirements to dimensional tolerances. Providing thorough specifications reduces the risk of miscommunication, which can lead to costly mistakes.
Quality Control Measures Throughout the Process
Incorporating quality control measures at different stages of the mold making process can significantly enhance the final product’s quality. This includes preliminary checks during design, mid-production inspections, and final evaluations before delivery.
Future Trends in Injection Molding and Mold Making
The field of injection molding and mold making is continuously evolving, influenced by advancements in technology, materials, and industry practices. Here are some future trends shaping this area:
Advancements in Materials and Technology
New materials, such as biodegradable plastics and advanced composites, are emerging, prompting mold makers to adapt their designs and processes. Additionally, technologies like 3D printing are gaining traction, allowing for more intricate and customized molds to be created swiftly and with less material waste.
Sustainability Practices in Mold Making
Growing environmental concerns are leading to increased demand for sustainable practices in mold making. This includes using recyclable materials, minimizing waste during production, and implementing energy-efficient processes.
The Role of Automation in Injection Molding
Automation is transforming the injection molding landscape, improving efficiency and reducing labor costs. Automated processes—from mold design through production—enhance precision and can enable more rapid scaling of production with fewer errors.