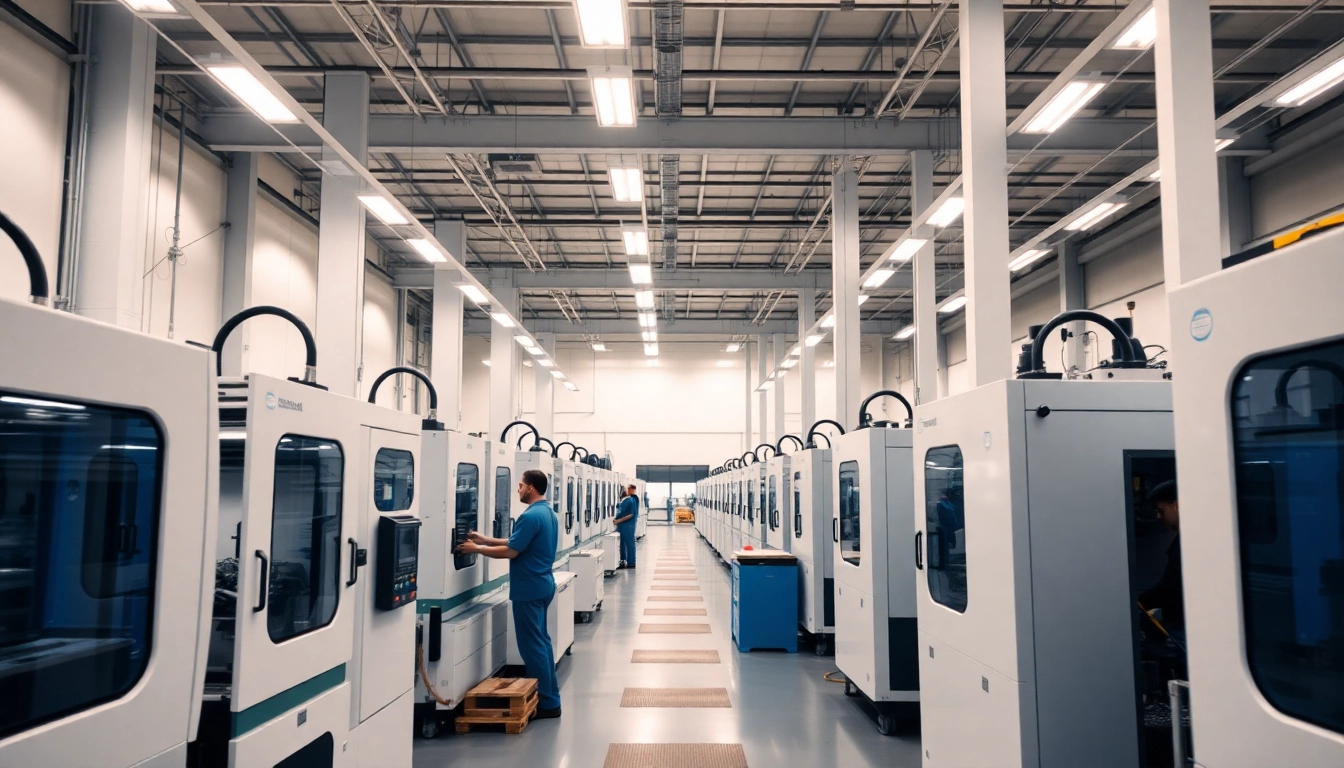
Understanding Injection Molding Processes
What Is Injection Molding?
Injection molding is a highly versatile manufacturing process used to produce parts by injecting molten material into a mold. This technique is particularly prevalent in the production of plastic components, although it can also be applied to metals, glass, and ceramics. The process involves heating the material until it becomes pliable and then injecting it under pressure into a mold cavity, where it cools and solidifies into the desired shape. This method is highly efficient, capable of producing complex shapes with high precision and repeatability.
Types of Injection Molding Techniques
Injection molding techniques can be broadly categorized into several types, each suited for specific applications:
- Thermoplastic Injection Molding: Utilizes thermoplastics, which can be heated and molded multiple times without degradation.
- Thermoset Injection Molding: Involves thermosetting materials that, once molded and cured, cannot be remolded. These materials are used where durability and high-temperature resistance are necessary.
- Multi-component Injection Molding: Combines two or more materials to produce parts with different properties within the same item.
- Gas-Assisted Injection Molding: Uses gas to void parts of the mold, which helps in reducing weight and improving surface finish.
- Co-Injection Molding: Involves injecting two different plastics simultaneously to enable complex designs with various properties.
Applications Across Industries
Injection molding is employed across a diverse range of industries, demonstrating its flexibility and efficiency. Key applications include:
- Automotive: Used for producing components such as dashboards, panels, and various fittings that require durability and aesthetic appeal.
- Consumer Goods: Produces everyday items like containers, toys, and household appliances.
- Medical: Essential for durable, high-quality components in medical devices, including syringes and IV connectors.
- Electronics: Critical for creating housings and internal components in electronic devices, where precision and safety are paramount.
Choosing the Right Injection Molding Company
What to Look for in a Manufacturer
When selecting an injection molding company, it’s crucial to consider several factors that can significantly impact your project’s success:
- Experience: A company with a proven track record in your industry can deliver better insights and products.
- Technical Expertise: Evaluate their capabilities in design and engineering, including the technology they use for injection molding.
- Customization: The ability to tailor solutions to meet specific needs is essential, especially for unique applications.
- Quality Assurance: Look for companies that implement robust quality control processes to ensure high-quality outputs.
Evaluating Company Certifications
Certifications can provide insights into a company’s commitment to quality and industry standards. Some important certifications to consider include:
- ISO 9001: Indicates a company’s quality management system is well established and consistently delivers products that meet customer expectations.
- ISO 13485: Focuses on medical device quality management systems, indicating the company’s capability to produce quality medical components.
- UL Certification: Ensures compliance with high safety standards for certain plastic materials used in various applications.
Comparing Costs and Services
Cost analysis doesn’t simply involve looking at the price per piece produced but requires evaluation of the overall value provided. When comparing various injection molding companies, consider:
- Unit Price: While important, the lowest price is not always the best option considering quality, material, and production reliability.
- Initial Setup Costs: This includes mold design and manufacturing, which may differ significantly between companies.
- Lead Time: Understanding the timeframe from the initial design stage to final production can affect project timelines.
Benefits of Using Injection Molding Services
Cost-Effectiveness Over Time
One of the premier benefits of injection molding is its cost-effectiveness in large-volume production. Although the initial setup and tooling costs can be high, the per-unit cost decreases significantly as quantity increases due to the efficiency of the process. This makes injection molding particularly attractive for producing high volumes of identical parts.
Quality and Precision in Production
Injection molding allows for the creation of parts with high precision and repeatable quality, thanks in part to automated processes and advanced machinery. Consistent wall thicknesses, clean edges, and intricate design capabilities contribute to superior quality, which is vital in competitive industries.
Scalability for Large Projects
Injection molding is exceptionally scalable, making it ideal for projects ranging from small batches to large-scale mass production. Companies can easily adjust production speeds and processes in response to market demands without significant overhauls of equipment or processes, allowing for rapid responses to changing needs.
Industry Trends Shaping Injection Molding
Advancements in Technology
The future of injection molding is being shaped by numerous technological advancements, including:
- Industry 4.0: Incorporating smart technology such as IoT and AI into production processes enhances operational efficiency, predictive maintenance, and data analytics.
- 3D Printing: Although traditionally separate, 3D printing is beginning to complement injection molding processes by allowing rapid prototyping and tooling adjustments.
- Robotics: Robots are increasingly used to handle repetitive tasks, improve speed, and enhance safety in manufacturing environments.
Eco-Friendly Practices
Environmental considerations are becoming increasingly relevant in injection molding. Companies are adopting eco-friendly practices, including:
- Biodegradable Materials: Many manufacturers are turning to sustainably sourced biodegradable plastics to reduce environmental impacts.
- Recycling Initiatives: Implementing recycling programs that allow leftover materials from production to be reprocessed and reused.
- Energy Efficiency: Upgrading machinery to energy-efficient models to lower carbon footprints and operational costs.
Custom Material Innovations
The advent of new materials is revolutionizing injection molding capabilities. Innovations in composite and engineered materials allow for:
- Lightweight Components: Advanced materials enable manufacturers to create lighter components without sacrificing strength.
- Enhanced Durability: Improved material properties result in longer-lasting products that maintain performance under stress.
- Customized Material Properties: New advancements allow for adjustments to material properties, enabling tailored solutions for specific needs.
Maximizing Success with Your Injection Molding Projects
Planning Your Project for Success
Effective planning is critical to a successful injection molding project. Key steps include:
- Define Your Objectives: Be clear about product goals, target audience, and overall project scope.
- Engage Early with Manufacturers: Consultation with potential manufacturers can provide insights into feasibility and design considerations.
- Market Research: Understanding market demands and benchmarks can guide design decisions and production methods.
Common Challenges and Solutions
Despite its many advantages, injection molding does come with challenges. Common issues include:
- Mold Making Delays: Ensure proper timelines are set in discussing mold creation to avoid project delays.
- Material Limitations: Work closely with suppliers to select the best materials that meet both budgetary and performance needs.
- Quality Control Issues: Implement stringent quality assurance protocols to catch defects early in the production process.
Measuring Performance and Quality Assurance
To assess the success of injection molding projects, it is essential to use performance metrics, such as:
- Defect Rates: Monitor the percentage of defective items produced and implement corrective actions when necessary.
- Cycle Times: Track production cycle times to understand efficiency and identify bottlenecks.
- Customer Feedback: Collect feedback from customers to improve product designs and address service delivery gaps.